Description
What is solvent recycler machine?
In the realm of industrial cleaning solutions, the solvent recycling machine stands tall, revolutionizing the way we handle used cleaning solvents. This sophisticated apparatus employs distillation to meticulously extract soils, debris, and oils from previously used solvents, paving the way for their renewed application. The impact is profound, with the potential to slash solvent purchases by a staggering 95% and curtail chemical waste disposal costs by over 90%.
Ready to start your solvent recovery project? Discover the excellence of our solvent recycling systems – reach out to us today!
Technical Parameter
Model | T-20EX | T-40EX | T-60EX | T-90EX | T-125EX | T-250EX | T-400EX |
Feed Capacity(L) | 20 | 40 | 60 | 90 | 125 | 250 | 400 |
Power(kW) | 2 | 4 | 4 | 5 | 6 | 16 | 32 |
Processing Time(Hour) | 1.5-2 | 2-2.5 | 2.5-3 | 3-3.5 | 3.5-4 | 3-4 | 4-6 |
Temperature Range(℃) | 50-210 | ||||||
Power Supply (ACV) | 220 | 380 | |||||
Recovery(%) | 95 | ||||||
Dimension(mm) | 850*600*1200 | 1020*750*1270 | 1020*750*1300 | 1160*870*1260 | 1180*850*1430 | 2600*1200*1950 | 3380*1470*2950 |
Weight(kg) | 100 | 140 | 150 | 170 | 200 | 520 | 1000 |
Labonsale Solvent Recycler Features
*Normal pressure work
*Whole machine Explosion-proof
*Solvent Recovery does not change chemical composition(The physical method of distillation, heating, condensation, and recovery is adopted without changing the chemical composition of the original solvent.)
*120° rotating slag discharge(The solvent recovery machine adopts a 120-degree rotating slag discharge design, which can be easily operated by one person, and is simple and convenient.)
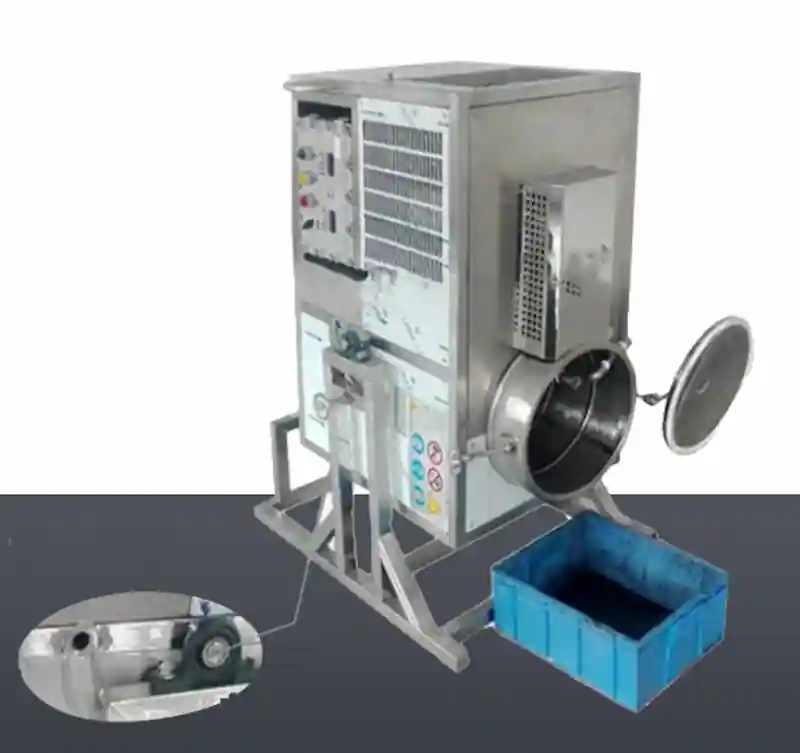
*Multi-stage temperature control
*High-temperature protection
*Stainless steel material
*Temperature-controlled shutdown
*Scheduled shutdown
*Low failure rate
How Does a Solvent Recycler Machine Work?
Solvent recovery systems employ the distillation process to separate volatile and nonvolatile solutions within a solvent. The solution undergoes boiling, and the resulting vapors are condensed back into liquid within a separate tank, akin to the operation of a vapor degreaser. The diverse components of the solvent and contaminants have distinct boiling points; typically, oils and soils have much higher temperatures than solvents. A practical example is the use of paint thinner for cleaning paint off paint guns and parts. In this case, the solvent boils at a lower temperature than the paint. Consequently, when the mixture is boiled, it leads to the condensation of pure solvent in one tank and the deposition of paint sludge components in another tank. Occasionally, a solvent recycling machine is also referred to as a paint-thinner recycler.
- Add the waste to be recycled;
- Use a rag to wipe the edge of the recycling barrel mouth wall and the surface of the fuselage clean;
- Close the lid of the barrel, and loosen the hot kerosene vent valve;
- Place a clean recycling bucket at the solvent outlet of the recycling machine, in which the clean solvent will be retained after recycling;
- Turn on the working switch of the recycling machine to make the equipment start to work;
- After the solvent recovery is completed, clean up the residue in the recovery bucket;
- Clean up equipment surface hygiene;
- Collect the recovered solvent;
Solvent Recycler Application Cases
- Automobile manufacturing and auto parts industry: Waste solvents generated during the cleaning of spraying equipment, such as thinners, gun cleaning water, tinas water, toluene, methyl ethyl ketone, etc.; waste solvents such as aviation kerosene, hydrocarbon cleaning agents, etc. generated during the cleaning of automobile parts.
- Sheet metal manufacturing, precision instruments: Waste solvents generated when cleaning products and equipment, such as alcohol, isopropyl alcohol (IPA) hydrocarbons, gasoline, trichlorethylene, etc.
- Packaging industry and printing industry: Gun washing water produced during spraying of packaging containers: screen washing water, plate washing water, car washing water, toluene, ethyl ester, etc. produced by printing and cleaning stencils and machines.
- Tut, paint and coating: During the production process of paints and coatings, various organic solvents and paint mixers such as production equipment, containers and filling equipment are cleaned, such as Tianna water, xylene, methyl ethyl ketone, butyl ester, etc.
- Digital electrical and optical products: Solvents used in cleaning mobile phones, cameras, computers, TVs and other parts (components), such as absolute ethanol, isopropyl alcohol (IPA), trichlorethylene, etc.
- Furniture manufacturing and exhibition equipment industry: Organic solvents for cleaning spray equipment and mixing paint, such as: gun cleaning water, Tianna water, banana water, toluene, methyl ethyl ketone, acetone, etc.
- PCB manufacturing, SMT manufacturing: Screen washing water and plate washing water generated during the PCB printing process, waste alcohol, isopropyl alcohol (IPA), etc. generated during the SMT manufacturing process.
- Shoe material manufacturing, painted gold jewelry: Various organic solvents used for cleaning spraying equipment in shoe material manufacturing; organic solvents discarded during cleaning of shoe soles, shoe upper printing and other processes.
- Others: For other industries not listed, please contact our technical staff.
Vacuum Assisted Distillation
Applying a vacuum to the distillation column and chamber may be necessary when dealing with solvents with higher boiling points and greater vapor density (above 29 AMU – atomic mass units). This is particularly relevant for substances like xylenes, CFCs, and others that are heavier than air. In contrast, lighter-than-air solvents such as acetones, MEK (Methyl ethyl ketone/butanone), MPK (Methyl n-propyl Ketone), alcohols, etc., may not require the application of a vacuum for distillation.
Integration of Inline Vapor Degreaser
Although vapor degreasers naturally distill solvents, extending the life and reducing solvent consumption can be achieved by further distilling only the vapor degreaser boil sump. The automated incorporation of a solvent recovery system into a vapor degreaser is typically straightforward, requiring no modifications to the vapor degreaser itself. The process involves extracting from the drain of the boil sump and directing the distilled solvents into the rinse sump or water separator. Waste is then stored in the solvent recycler for convenient disposal. This enables continuous use of the degreaser without downtime for boil sump cleaning. With the implementation of solvent recovery systems, intervals for solvent boil-down and change-out can be extended by up to 200%.
The use of solvent recycling machines and solvent recovery systems can significantly reduce costs, hazardous waste disposal, and solvent consumption, all while enhancing process stability and overall operation efficiency.
Solvent recycler machine Application
Solvent recycler machine reduces chemical disposal costs and new solvent purchases. Solvent recycling equipment can recycle nearly any solvent or chemistry used in electroplating, metal finishing, paint and powder coating, parts washing, and vapor degreasing, including:
- Mineral spirits
- Paint Thinner
- Acetone
- IPA (isopropyl alcohol)
- MEK (methyl ethyl ketone)
- Xylene
- Hexane
- Various alcohols
- Chlorinated solvents (AK225, 1,2 trans-dichloroethylene / trans DCE, 3Mâ„¢ Novecâ„¢, Dupont Vertrel)
- Microcare solvents
- Terpenes Toluene
- Aromatic Solvents
Benefits of solvent recycler machine
- Substantially Reduces the need to purchase new solvents
- Reduce disposal cost
- ROI in a matter of Months
- Simplify regulatory reporting
- Improves control over hazardous waste liability
- Minimize on-site storage of hazardous wastes
- Saves your company tons of money
Go back to homepage
View more about Recycling on Wikipedia