In this comprehensive guide, we’ll delve into the world of vacuum drying ovens, exploring their benefits, operation, applications, and maintenance. Whether you’re a seasoned professional or new to the concept, these insights will empower you to make informed decisions and optimize your drying processes for superior results.
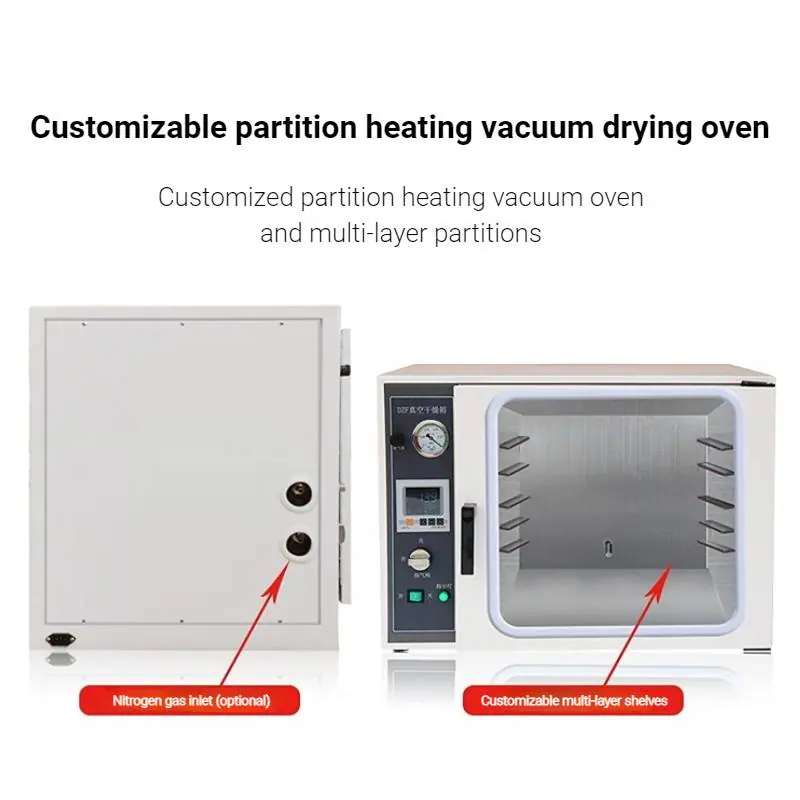
Mastering Vacuum Drying Ovens: A Comprehensive Guide to Techniques and Applications
Vacuum drying ovens, a crucial asset in numerous industries, offer a distinct advantage by efficiently eliminating moisture or solvents from materials under controlled pressure conditions. Whether you’re a seasoned professional or a newcomer, this comprehensive guide will delve into the realm of vacuum drying ovens, unveiling their advantages, operational methods, diverse applications, and essential maintenance. Embark on this enlightening journey to elevate your expertise and optimize your drying processes for exceptional outcomes.
Unveiling Vacuum Drying Techniques
Venture into the realm of vacuum drying, an indispensable method for extracting moisture or solvents from materials while operating under reduced pressure. Industries spanning from food processing, pharmaceuticals, and electronics to materials science rely on this technique. The primary objective of vacuum drying is to expedite evaporation by lowering the solvent’s boiling point. This gentler process ensures controlled drying without jeopardizing the material’s integrity.
Let’s explore the core techniques of vacuum drying:
Types of Vacuum Drying Techniques:
1. Vacuum Drying Oven
This method entails placing the material within a vacuum chamber on trays. Through the application of heat and vacuum, moisture evaporation accelerates. Vacuum tray drying caters to solids, powders, and granular materials, making it versatile for various applications.
2. Vacuum Freeze Drying (Lyophilization)
Ideal for delicate materials like pharmaceuticals, biological samples, and food, this technique involves freezing the material. Subsequently, a vacuum removes moisture through sublimation, bypassing the liquid phase.
3. Rotary Evaporators
For liquid drying on a smaller scale, rotary evaporators shine. By placing the material in a rotating flask, heat prompts evaporation under reduced pressure. Condensation and collection follow, ensuring efficient liquid drying.
4. Vacuum Belt Drying
A conveyor belt ushers the material through a vacuum chamber while heat is applied. This continuous process is well-suited for thin materials like sheets or films.
Advantages that Set Vacuum Drying Apart
Venturing into vacuum drying brings forth a plethora of benefits that distinguish it from conventional drying methods:
Gentle Drying
Materials benefit from lower temperatures, preserving their quality and characteristics intact.
Accelerated Drying
Reduced boiling points expedite the evaporation process, ensuring swifter results.
Uniform Drying
Even heat distribution due to vacuum assistance leads to consistent and thorough drying.
Navigating Considerations and Overcoming Challenges
While vacuum drying offers a multitude of advantages, certain factors warrant consideration:
- Equipment Investment:Installation and maintenance of vacuum drying setups can be substantial.
- Precision Control:Achieving optimal drying necessitates precise control over vacuum levels and temperatures.
- Material Specificity:Diverse materials demand tailored vacuum drying conditions to avoid damage and yield desired outcomes.
In summary, vacuum drying techniques are valuable tools for removing moisture or solvents from various materials in a controlled and efficient manner. The choice of technique depends on the type of material being dried, its sensitivity to temperature, and the desired end result.
Choosing Your Ideal Vacuum Drying Oven
Selecting the right vacuum drying oven necessitates careful deliberation. Here’s a roadmap to guide your decision:
- Drying Requirements: Understand the characteristics of the materials you intend to dry:
- What is the material’s composition?
- Is it heat-sensitive or prone to degradation?
- What is the moisture content you need to achieve?
- Temperature Range: Ensure the vacuum drying oven can reach and maintain the required temperature range for your application. Some ovens offer precise temperature control and programmable settings.
- Vacuum Level: Different materials require specific vacuum levels. Choose an oven with a vacuum pump that can achieve the necessary pressure for efficient drying.
- Capacity and Size: Consider the volume of material you’ll be drying and choose an oven with an appropriate chamber size. This ensures optimal space utilization and efficient drying.
- Heating Technology: Look for ovens with advanced heating technology, such as evenly distributed heating elements, to ensure uniform drying throughout the chamber.
- Controls and Programming: User-friendly controls and programmable features can enhance your ability to customize drying cycles for different materials.
- Safety Features: Prioritize ovens with safety mechanisms like over-temperature protection, pressure relief valves, and alarms to prevent accidents and ensure operator safety.
- Material Compatibility: Verify that the oven’s construction materials are compatible with your drying substances to prevent contamination or reactions.
- Ease of Maintenance: Opt for an oven with easy-to-clean surfaces and accessible components for convenient maintenance.
- Energy Efficiency: Select an oven with energy-efficient features, insulation, and digital controls to optimize power consumption.
- Brand Reputation and Support: Choose a reputable manufacturer known for producing reliable vacuum drying ovens. Good customer support and available spare parts are essential for long-term use.
- Budget Considerations: While cost is a factor, prioritize the oven’s suitability for your application and long-term value over the initial investment.
- Optional Accessories: Some ovens offer additional features like shelves, trays, or specialized racks for different types of materials.
- User Reviews and Recommendations: Research user reviews and seek recommendations from colleagues or experts in your field who have experience with vacuum drying ovens.
- Warranty and Service: Check the warranty period and the availability of service and technical support.
Remember that selecting the right vacuum drying oven involves assessing your specific drying needs, considering the technical specifications, and weighing the features that best align with your application’s requirements. Taking the time to research and make an informed decision will help you achieve optimal results and maximize the efficiency of your drying processes.
Key Components and Operation of Vacuum Drying Ovens
Key Components of Vacuum Drying Ovens:
- Vacuum Chamber: This is the main compartment where the material to be dried is placed. It is designed to create a sealed environment for the drying process under reduced pressure conditions.
- Heating Elements: These elements provide the necessary heat to the chamber for the evaporation of moisture or solvents from the material. They are typically located on the walls or floor of the chamber.
- Vacuum Pump: The vacuum pump is responsible for reducing the pressure inside the chamber, creating a vacuum environment. This allows for lower boiling points and faster evaporation.
- Temperature and Pressure Controls: These controls allow you to set and monitor the temperature and pressure within the chamber. They ensure precise and consistent drying conditions.
- Gauges and Sensors: Gauges display the vacuum level and temperature, while sensors provide real-time data to ensure accurate control of the drying process.
- Safety Features: Over-temperature protection, pressure relief valves, and alarms are crucial safety components that prevent overheating, excess pressure, and potential hazards.
- Shelves or Trays: These are used to hold the material being dried. They are designed to allow uniform heat distribution and efficient drying.
- Insulation: High-quality insulation materials are used to minimize heat loss and maintain stable drying conditions within the chamber.
- Door and Sealing Mechanism: The door of the vacuum drying oven must have a secure sealing mechanism to maintain the vacuum and prevent air leakage during the drying process.
Operation of Vacuum Drying Ovens:
- Loading: Place the material to be dried on the shelves or trays inside the vacuum chamber. Ensure that the material is spread out evenly and does not obstruct airflow.
- Sealing: Close and secure the oven door tightly to create a sealed environment within the chamber.
- Setting Parameters: Set the desired temperature and pressure levels on the control panel. You can also program specific drying cycles if the oven supports programmable features.
- Start Heating: Turn on the heating elements to raise the temperature within the chamber. As the temperature increases, moisture or solvents in the material start evaporating.
- Vacuum Pump: Activate the vacuum pump to reduce the pressure inside the chamber. The lower pressure lowers the boiling point of the solvents, facilitating faster evaporation.
- Drying Process: Monitor the temperature and vacuum levels throughout the drying process. The material will gradually lose moisture as it evaporates. The vacuum environment prevents the material from overheating.
- Completion: Once the material reaches the desired level of dryness, stop the heating and vacuum pump. Allow the chamber to cool down before opening the door.
- Unloading: Carefully remove the dried material from the oven. Ensure that the material has cooled sufficiently before handling.
- Maintenance: Regularly clean the vacuum drying oven, including the chamber, shelves, and seals. Check and replace any worn-out components to maintain optimal performance.
Vacuum drying ovens provide a controlled and efficient method for removing moisture or solvents from various materials. Proper understanding of the key components and careful operation is essential to achieve consistent and reliable drying results.
Step-by-Step Guide to Efficient Vacuum Drying
- Preparation:a. Material Selection: Choose the material to be dried and ensure it’s properly prepared for the process. Understand its characteristics, moisture content, and any specific requirements.b. Equipment Check: Ensure the vacuum drying oven is clean, properly maintained, and all components are in working condition.
- Loading the Oven:a. Arrangement: Place the material evenly on the drying shelves or trays inside the vacuum chamber. Avoid overcrowding to allow proper airflow.b. Uniformity: Arrange the material to ensure uniform heat distribution and efficient drying. Consider using additional accessories like trays or racks if needed.
- Sealing and Setting Parameters:a. Door Closure: Close and secure the oven door tightly to create an airtight seal.b. Temperature: Set the desired drying temperature on the control panel. Ensure the chosen temperature is appropriate for the material and its sensitivity.c. Pressure: Set the vacuum level according to the material’s requirements. Consider the vapor pressure of the solvent or moisture being removed.d. Time: Program the desired drying time or duration based on the material’s characteristics and drying goals.
- Starting the Drying Process:a. Heating: Turn on the heating elements to initiate the temperature increase within the chamber. Gradually ramp up the temperature to the desired level to prevent thermal shocks.b. Vacuum Pump: Start the vacuum pump to reduce the pressure inside the chamber. Monitor and adjust the vacuum level as needed.
- Monitoring and Control:a. Real-time Data: Keep an eye on the control panel’s temperature and pressure readings. Ensure they remain within the set parameters.b. Adjustments: Make necessary adjustments to the temperature and vacuum settings if deviations occur. Maintain a stable and controlled drying environment.
- Drying Progress:a. Visual Inspection: Periodically inspect the material through the oven’s viewing window to monitor its drying progress. Look for changes in appearance or moisture content.b. Sampling: Consider taking occasional samples to assess the moisture content and ensure the material is drying as expected.
- Completion and Cooling:a. Drying Endpoint: Once the material reaches the desired moisture content or dryness level, stop the heating and vacuum pump.b. Cooling Down: Allow the chamber to cool down gradually before opening the door. Rapid cooling might lead to condensation on the material.
- Unloading and Handling:a. Material Removal: Carefully remove the dried material from the oven. Use appropriate tools if needed to prevent contamination.b. Cooling Period: Allow the material to cool completely before handling or packaging.
- Post-Drying Care:a. Cleaning: Clean the oven’s interior, shelves, and seals to maintain its efficiency and prevent cross-contamination.b. Maintenance: Regularly inspect and maintain the vacuum drying oven components, including seals, heating elements, and vacuum pump, to ensure consistent performance.
Efficient vacuum drying requires careful planning, precise parameter settings, continuous monitoring, and attention to detail. Following this step-by-step guide can help you achieve optimal drying results while preserving the quality of your materials.
Safety Measures and Maintenance for Vacuum Drying Ovens
Safety Measures for Vacuum Drying Ovens:
- Proper Ventilation: Ensure the drying area is well-ventilated to prevent the buildup of potentially harmful fumes or gases. This is especially important if volatile solvents are being dried.
- Fire Safety: Keep flammable materials and substances away from the drying area. Install fire extinguishers and ensure that all personnel are familiar with their locations and proper usage.
- Pressure Relief: Equip the vacuum chamber with pressure relief valves to prevent over-pressurization. These valves release excess pressure in case of a malfunction.
- Emergency Stop: Install an easily accessible emergency stop button near the oven’s control panel to quickly halt the drying process in case of an emergency.
- Operator Training: Ensure that all personnel operating the vacuum drying oven are properly trained in its usage, safety protocols, and emergency procedures.
- Personal Protective Equipment (PPE): Provide and mandate the use of appropriate PPE, such as safety goggles, gloves, lab coats, and closed-toe shoes, to protect against potential hazards.
- Electrical Safety: Regularly inspect power cords, plugs, and electrical connections for signs of wear or damage. Ensure the oven is properly grounded to prevent electrical accidents.
- Monitoring and Supervision: Maintain constant supervision during the drying process to promptly address any issues that may arise. Do not leave the oven unattended while in operation.
Maintenance for Vacuum Drying Ovens:
- Regular Cleaning: Routinely clean the interior of the vacuum chamber, shelves, and seals to prevent cross-contamination between different materials and maintain efficient drying.
- Seal Inspection: Check the door seal for any signs of wear or damage. A tight and intact seal is crucial to maintain the vacuum environment and prevent air leakage.
- Heating Elements: Inspect the heating elements for any signs of deterioration or malfunction. Replace damaged elements promptly to ensure uniform heating.
- Vacuum Pump Maintenance: Follow the manufacturer’s guidelines for vacuum pump maintenance. Regularly check for oil levels, filter condition, and any unusual noises or vibrations.
- Pressure Relief Valves: Test pressure relief valves periodically to ensure they are functioning properly. Replace any faulty valves promptly.
- Temperature and Pressure Calibration: Calibrate temperature and pressure sensors regularly to maintain accurate readings and ensure precise control over the drying process.
- Documentation: Keep detailed records of maintenance activities, repairs, and any issues encountered. This information helps track the oven’s performance and troubleshoot problems.
- Scheduled Inspections: Implement a schedule for comprehensive inspections and maintenance, including checking electrical components, safety features, and overall system performance.
- Spare Parts Inventory: Maintain a supply of essential spare parts, such as seals, gaskets, and heating elements, to facilitate timely repairs and minimize downtime.
- Professional Service: If you encounter complex issues or need major repairs, consult the oven’s manufacturer or a qualified service technician for assistance.
By following these safety measures and performing regular maintenance, you can ensure the safe and efficient operation of your vacuum drying oven while prolonging its lifespan and maintaining consistent drying results.
Common Challenges and Solutions in Vacuum Drying
- Uneven Drying:Challenge: Non-uniform drying can result from improper material placement or inadequate heat distribution.Solution:
- Arrange the material evenly on the drying shelves or trays.
- Use accessories like trays or racks to ensure uniform airflow.
- Implement proper oven calibration and ensure even heating element distribution.
- Condensation:Challenge: Condensation can occur when the dried material is exposed to cooler air after the drying process.Solution:
- Gradually reduce the vacuum level and temperature before opening the chamber to prevent sudden temperature changes.
- Allow the dried material to cool down within the vacuum chamber before removal.
- Overheating:Challenge: Excessive heat can lead to material degradation or even ignition in extreme cases.Solution:
- Monitor and control the temperature using the oven’s controls.
- Implement over-temperature protection mechanisms and alarms.
- Use temperature sensors to ensure precise and safe heating.
- Moisture Entrapment:Challenge: Some materials might trap moisture internally, leading to incomplete drying.Solution:
- Use proper drying techniques and duration to ensure thorough moisture removal.
- Consider pre-treatment methods like freeze drying to prevent moisture entrapment.
- Sealing Issues:Challenge: Air leaks through damaged or improper seals can compromise the vacuum environment.Solution:
- Regularly inspect and replace worn-out or damaged seals.
- Ensure the door is tightly closed and sealed before starting the drying process.
- Vacuum Pump Problems:Challenge: Vacuum pump malfunctions can affect the vacuum level and drying efficiency.Solution:
- Regularly maintain and service the vacuum pump as per manufacturer recommendations.
- Monitor pump performance and address any unusual noises or vibrations promptly.
- Material Degradation:Challenge: Some materials might degrade or change properties under vacuum and high-temperature conditions.Solution:
- Opt for lower drying temperatures when dealing with sensitive materials.
- Test and monitor the material’s behavior during the drying process.
- Long Drying Times:Challenge: Inefficient drying can lead to longer processing times and reduced productivity.Solution:
- Optimize vacuum and temperature settings for the specific material being dried.
- Consider using vacuum pumps with higher capacity for faster drying.
- Batch-to-Batch Variability:Challenge: Consistency between batches may be challenging to achieve.Solution:
- Maintain consistent parameter settings for each batch.
- Regularly calibrate temperature and pressure sensors.
- Safety Concerns:Challenge: Operating under vacuum conditions requires adherence to strict safety protocols.Solution:
- Train personnel on proper operation, emergency procedures, and use of personal protective equipment.
- Implement safety features like emergency stops, pressure relief valves, and alarms.
By being aware of these common challenges and implementing the suggested solutions, you can enhance the efficiency, reliability, and safety of vacuum drying processes.
Future Trends and Innovations in Vacuum Drying Processes
- Smart and Automated Drying:As automation and artificial intelligence continue to advance, vacuum drying processes may become more intelligent and automated. Smart sensors and control systems could monitor and adjust drying parameters in real-time, optimizing efficiency and ensuring consistent quality.
- Energy-Efficient Drying:Innovations in vacuum drying technology may focus on further reducing energy consumption. Improved insulation materials, heat recovery systems, and advanced heating methods could lead to more energy-efficient drying processes.
- Advanced Heating Technologies:Future vacuum drying processes might incorporate advanced heating methods, such as microwave or radiofrequency heating. These technologies can provide faster and more uniform drying by directly heating the material’s moisture content.
- Combined Drying Techniques:Hybrid drying methods that combine vacuum drying with other technologies, such as freeze drying or supercritical fluid extraction, could become more prevalent. These combinations could offer enhanced efficiency, reduced processing times, and better preservation of material properties.
- Customized Drying Cycles:Vacuum drying processes may become more customizable, allowing users to create specific drying profiles for different materials. This could lead to optimized drying results tailored to the unique characteristics of each substance.
- Nanotechnology and Thin Films:In the field of nanotechnology, vacuum drying could be utilized for precise control over the drying of nanomaterials and thin films. This could be essential for applications in electronics, coatings, and advanced materials.
- Green Drying Methods:Researchers may develop environmentally friendly drying techniques that minimize the use of solvents and reduce emissions. Vacuum drying processes could be designed to have a smaller ecological footprint and contribute to sustainable manufacturing practices.
- Real-time Monitoring and Feedback:Vacuum drying ovens may incorporate real-time monitoring technologies that provide detailed insights into the drying process. This information could be used for immediate adjustments, quality control, and process optimization.
- Innovative Materials and Applications:As new materials emerge, vacuum drying processes could adapt to accommodate their unique properties. This might include specialized techniques for drying biomaterials, pharmaceuticals, advanced composites, and more.
- Miniaturized and Portable Systems:The development of smaller, portable vacuum drying systems could enable on-site drying for various applications, such as in remote locations, laboratories, and field operations.
- Waste Reduction and Circular Economy:Vacuum drying processes might play a role in reducing waste and promoting a circular economy by enabling the recovery of valuable components from waste materials.
- Process Modeling and Simulation:Advanced computational modeling and simulation tools could be used to predict and optimize vacuum drying processes, reducing the need for extensive trial-and-error experimentation.
The future of vacuum drying processes holds exciting possibilities for increased efficiency, sustainability, and adaptability to diverse applications. Continued research and development in this field will likely lead to innovative solutions that address evolving industry needs.
View more about Vacuum Drying on Wikipedia