In the realm of industrial processes, spray drying stands as a vital technique that converts liquid substances into powdered forms. Whether you’re in the food, pharmaceutical, or chemical industry, selecting the perfect spray dryer is paramount to achieving optimal results. This comprehensive guide delves into the intricacies of choosing the right spray dryer for your needs. From understanding capacity and atomization to evaluating energy efficiency and manufacturer reputation, we’ll cover all aspects to ensure you make an informed decision.
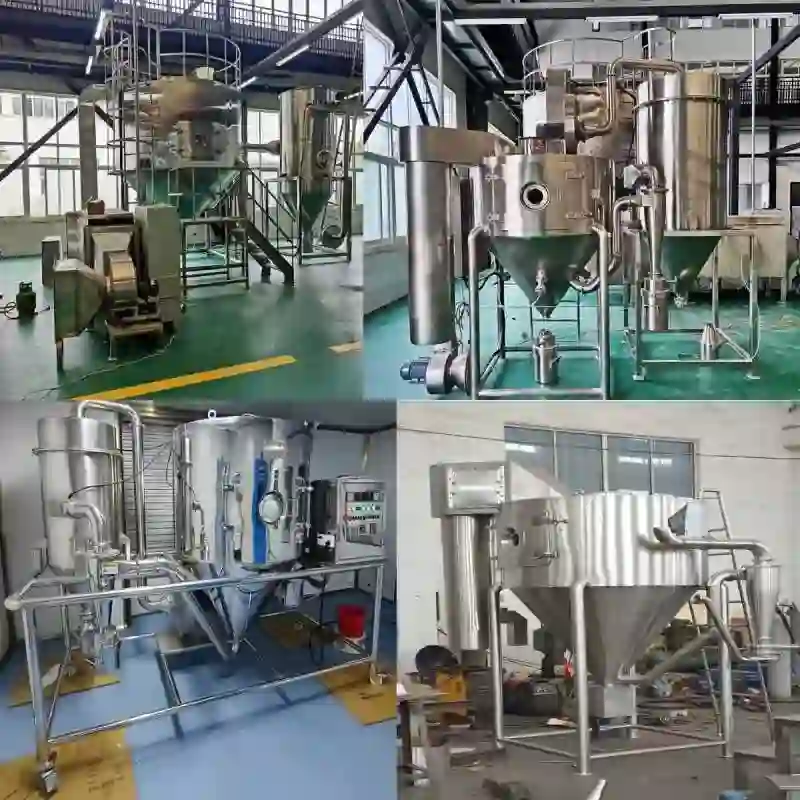
Introduction to Spray Dryers: Exploring the Basics
Spray dryers are essential equipment widely used in various industries for converting liquid substances into powdered form. This versatile technology finds applications in fields such as food, pharmaceuticals, chemicals, ceramics, and more. In this overview, we’ll delve into the fundamental principles of spray dryers and how they work.
Principle of Operation:
At its core, a spray dryer operates on the principle of atomization and evaporation. It converts a liquid feed into a fine spray of droplets, which are then exposed to a stream of hot air. This rapid contact between the droplets and the hot air causes the solvent (liquid component) to evaporate, leaving behind solid particles that form the desired powder.
Components of a Spray Dryer:
1.Feed System: The liquid feedstock, which can be a solution, suspension, or emulsion, is introduced into the spray dryer. It is crucial to atomize the feed into small droplets to ensure efficient drying.
2.Atomization Mechanism: The atomization process breaks down the liquid into tiny droplets. There are various methods of atomization, including rotary atomizers, pressure nozzles, and centrifugal atomizers. These mechanisms determine the size and distribution of droplets, which impacts the final product’s characteristics.
3.Drying Chamber: This is where the magic happens. The chamber is exposed to a flow of hot air, which acts as the drying medium. The hot air quickly absorbs the solvent from the droplets, causing them to shrink and solidify into powder particles.
4.Hot Air System: A heat source, such as a heater or a steam generator, generates the hot air. The temperature and flow rate of the hot air are critical parameters that influence the drying process and the quality of the final product.
5.Powder Collection System: Once the droplets are dried and converted into powder particles, they need to be collected. Cyclones, bag filters, and electrostatic precipitators are common methods for separating the powder from the exhaust air.
Types of Spray Dryers: Co-current, Counter-current, and Mixed-Flow
1.Co-current Spray Dryer:
In a co-current spray dryer, both the atomized liquid droplets and the drying air flow in the same direction. This means that the droplets enter the dryer chamber at the top, and as they travel downward, they are exposed to progressively hotter air. The evaporation process takes place as the droplets move through the drying chamber. Co-current spray dryers are often used when dealing with heat-sensitive materials, as the lower inlet temperature can help prevent product degradation.
2.Counter-current Spray Dryer:
In a counter-current spray dryer, the atomized liquid droplets and the drying air flow in opposite directions. The droplets are introduced at the top of the drying chamber, while the hot drying air is introduced at the bottom. As the droplets fall, they encounter the hottest air first and gradually cooler air as they descend. Counter-current spray dryers are commonly used for heat-stable materials, as the higher inlet temperatures can result in better drying efficiency.
3.Mixed-Flow Spray Dryer:
A mixed-flow spray dryer is a combination of both co-current and counter-current designs. In this type, the atomized liquid droplets and the drying air flow diagonally or at various angles to each other within the drying chamber. This design aims to achieve a balance between the advantages of both co-current and counter-current configurations, providing versatility in terms of drying efficiency and heat sensitivity.
Each type of spray dryer has its own set of advantages and limitations, making them suitable for different applications and materials. The choice of spray dryer type depends on factors such as the nature of the material being dried, desired drying efficiency, heat sensitivity, and overall process requirements.
Factors Influencing Spray Drying:
Several factors play a role in successful spray drying:
1.Feed Properties: The composition, viscosity, and solids content of the liquid feed affect droplet formation and drying efficiency.
2.Atomization: The atomization method and nozzle design determine droplet size distribution, which impacts the powder’s characteristics.
3.Airflow and Temperature: The temperature and airflow rate of the hot air control drying kinetics and particle morphology.
4.Residence Time: The time it takes for droplets to travel through the drying chamber affects the final moisture content and particle size.
5.Equipment Design: The design of the drying chamber, feed system, and powder collection system influences overall efficiency and product quality.
Advantages of Spray Drying:
1.Preservation of Heat-Sensitive Materials: Spray drying allows heat-sensitive materials to be converted into powder without significant degradation.
2.Particle Size Control: By adjusting atomization and drying parameters, manufacturers can control particle size distribution, leading to consistent product quality.
3.Enhanced Solubility: The increased surface area of powdered particles often results in improved solubility.
4.Customization: Spray drying can be tailored to produce different particle shapes and densities to meet specific application requirements.
In conclusion, spray dryers are pivotal tools in modern industrial processes, offering a method to transform liquids into powders while maintaining product integrity. Understanding the underlying principles and factors influencing spray drying helps optimize the process for desired outcomes across various industries.
Innovations in Spray Drying Technology:
Spray drying is a widely used technique in various industries for converting liquid substances into dry powders. Over the past few years, there have been notable innovations in spray drying technology that have improved efficiency, product quality, and versatility. Some of these advancements include:
1.Advanced Nozzle Designs: Nozzles play a crucial role in spray drying as they determine droplet size and distribution. Recent innovations have led to the development of precision-engineered nozzles that can produce uniform droplets, resulting in improved powder quality and reduced waste.
2.Drying Chamber Modifications: The design of the drying chamber has been optimized to enhance heat and mass transfer efficiency. Innovative airflow patterns and heat distribution systems ensure better control over drying parameters, leading to higher product yields and reduced energy consumption.
3.Integrated Process Control: Automation and real-time monitoring have become integral to modern spray drying systems. Advanced sensors and control algorithms allow for precise adjustments of temperature, airflow, and feed rate, ensuring consistent product quality and minimizing variations.
4.Hybrid Drying Technologies: Combining spray drying with other drying methods like fluid bed drying or freeze drying has led to hybrid systems with enhanced capabilities. These systems can capitalize on the strengths of each method, resulting in products with improved solubility, stability, and texture.
5.Nanoencapsulation: Spray drying has been adopted for the encapsulation of nanoparticles and sensitive compounds. This innovation has enabled the controlled release of active ingredients in various applications, such as pharmaceuticals, food, and cosmetics.
Future Trends Shaping the Evolution of Spray Dryers:
Looking ahead, several trends are expected to shape the evolution of spray drying technology:
1.Sustainability: The industry is moving towards greener and more sustainable practices. Future spray dryers are likely to focus on reducing energy consumption, minimizing waste, and using environmentally friendly solvents.
2.Customization and Flexibility: Manufacturers are seeking spray drying solutions that can accommodate a wider range of materials and product specifications. Future spray dryers may offer greater flexibility through modular designs and adaptable process parameters.
3.Continuous Spray Drying: While traditionally a batch process, there’s a growing interest in developing continuous spray drying systems. These systems could offer improved efficiency, reduced labor requirements, and seamless integration into automated production lines.
4.Improved Particle Engineering: Innovations in particle engineering techniques will enable the production of powders with precisely controlled particle sizes, morphologies, and surface properties. This level of control is vital for tailoring products to specific applications.
5.Advanced Computational Modeling: Computational fluid dynamics (CFD) simulations will become more sophisticated, aiding in the design and optimization of spray drying processes. These simulations will provide insights into fluid behavior, droplet dynamics, and drying kinetics.
6.Application Expansion: Spray drying is extending beyond traditional industries such as food and pharmaceuticals. It’s finding applications in areas like 3D printing, advanced materials, and energy storage, driving the need for specialized spray drying solutions.
7.Industry 4.0 Integration: The integration of Industry 4.0 concepts will lead to “smart” spray dryers capable of real-time monitoring, data analysis, and autonomous adjustments. This will further enhance product quality, consistency, and process efficiency.
In conclusion, innovations in spray drying technology are rapidly evolving to meet the demands of various industries. With a focus on efficiency, sustainability, and customization, the future of spray drying holds exciting possibilities for producing high-quality powders across a diverse range of applications.
Factors to Consider When Choosing a Spray Dryer
When embarking on the journey to select the ideal spray dryer, various factors come into play:
Spray Dryer Capacity and Throughput
Determining the appropriate capacity and throughput of a spray dryer is crucial for maintaining production efficiency. Consider the volume of liquid to be processed and the desired powder output rate. Oversized dryers can lead to unnecessary energy consumption, while undersized ones might hinder your production goals.
Heating Method and Temperature Control
The choice of heating method, whether it’s direct or indirect, impacts the product’s quality and the dryer’s efficiency. Temperature control is vital to avoid thermal degradation of the material being dried. Modern spray dryers offer advanced temperature regulation systems that ensure consistent and precise drying conditions.
Nozzle Types and Atomization
The atomization process plays a pivotal role in spray drying, influencing particle size and uniformity. Nozzle types, such as pressure nozzles or rotary atomizers, offer distinct advantages. Understanding their impact on droplet formation aids in achieving the desired powder characteristics.
Airflow Design and Patterns
Efficient airflow distribution within the dryer chamber promotes even drying and prevents agglomeration. Co-current and counter-current airflow patterns each have their benefits. Proper design of air dispersion plates and exhaust systems ensures optimal drying performance.
Material Compatibility and Product Quality
Different materials have varying drying requirements and susceptibility to thermal stress. Compatibility between the material and the dryer construction material is crucial to avoid contamination. Moreover, selecting a dryer that preserves product quality, such as flavor or active ingredient potency, is paramount.
Energy Efficiency and Operating Costs
Energy-efficient dryers not only reduce operational costs but also contribute to sustainability efforts. Consider dryers with heat recovery systems, which recycle excess heat for the drying process. Evaluating operating costs over the machine’s lifespan aids in making financially sound decisions.
Maintenance and Cleanability
Regular maintenance is essential to extend the spray dryer’s lifespan and ensure consistent performance. Opt for designs that facilitate easy access to critical components for cleaning and maintenance. This not only reduces downtime but also enhances product safety.
Selecting Additional Features
Spray dryers often come with various additional features that cater to specific industry needs. These include features like inert gas flushing for oxygen-sensitive products or integrated particle collection systems. Choosing the right features can enhance overall process efficiency.
Evaluating Manufacturer Reputation
The reputation of the manufacturer speaks volumes about the quality of their products. Research the manufacturer’s history, customer reviews, and industry standing. A reputable manufacturer is more likely to provide reliable equipment and excellent customer support.
Steps to Optimal Spray Dryer Selection
1.Define Your Requirements: Clearly outline your production goals, material characteristics, and quality standards.
2.Conduct Market Research: Explore the available spray dryer options, considering various manufacturers and their offerings.
3.Prioritize Factors: Rank the factors discussed earlier based on their importance to your specific application.
4.Budget Analysis: Determine the budget you’re willing to allocate for the spray dryer investment and factor in operational costs.
5.Consult Experts: Engage with industry experts or consultants to gain insights into the latest trends and best practices.
6.Request Proposals: Reach out to selected manufacturers for detailed proposals based on your requirements.
7.Compare and Analyze: Compare the proposals, considering technical specifications, features, and pricing.
8.Site Visit: If possible, visit the manufacturer’s facilities to witness the production process and quality standards firsthand.
9.Finalize Your Choice: Select the spray dryer that aligns best with your needs, considering performance, features, and cost.
10.Negotiate and Purchase: Negotiate the terms of purchase, warranty, and after-sales support before finalizing the deal.
Conclusion
In conclusion, selecting the perfect spray dryer requires a comprehensive understanding of your application’s specific needs and the available options in the market. By considering factors such as material properties, production capacity, particle size requirements, energy efficiency, and maintenance, you can make an informed decision that aligns with your goals.
Ensure you assess the construction, material, airflow systems, control features, and associated costs before making your final choice. By following this guide, you’ll be better equipped to navigate the complexities of selecting a spray dryer that optimally suits your production needs and contributes to your business’s success.
FAQs
1.What industries benefit from spray dryers?
Spray dryers find applications in various industries, including food, pharmaceuticals, chemicals, and ceramics, where converting liquids into powders is essential.
2.What are the key factors affecting spray dryer selection?
Material properties, production capacity, particle size requirements, heat sensitivity, energy efficiency, and maintenance considerations are vital factors.
3.Can I get assistance with spray dryer installation and training?
Yes, many manufacturers offer on-site installation, operator training, and ongoing technical support to ensure optimal performance.
4.How do I calculate the return on investment for a spray dryer?
Calculate the initial investment, operating costs, and potential increase in production efficiency or product quality to determine the ROI.
5.Where can I learn more about available spray dryer options?
Access a range of spray dryer options and in-depth information at Labonsale.
View more about Spray Drying on Wikipedia