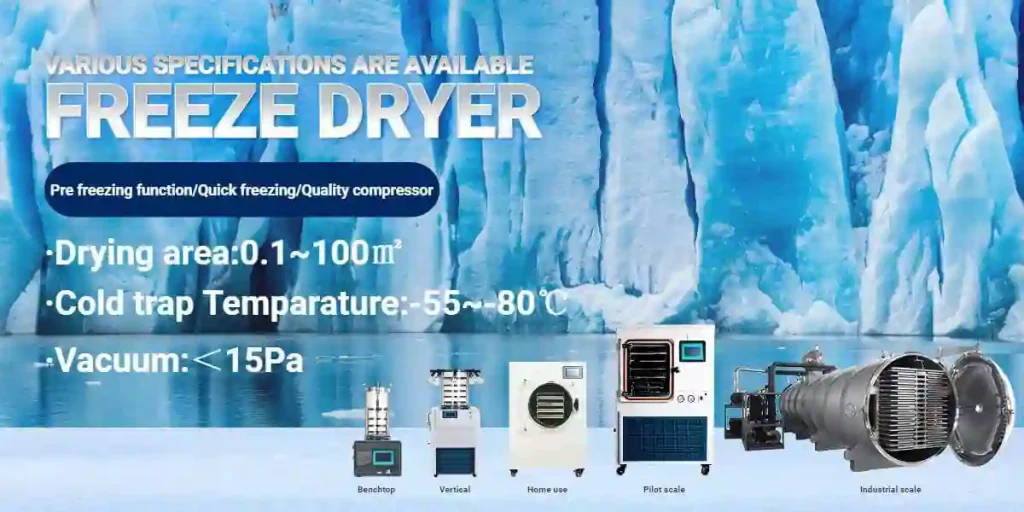
Science Behind Lyophilizer
Unveiling the Science Behind Lyophilizer: Exploring Phases, Pressure, and Quality Preservation
The intricacies of Lyophilization, a remarkable process also known as freeze-drying, lie at the heart of scientific exploration and preservation. This article delves into the phases of the Freeze-Drying Process, the role of Pressure and Temperature, and the unparalleled Preservation of Structure and Quality.
Decoding the Phases of Freeze-Drying Process
The Freeze-Drying Process encompasses three pivotal phases: Freezing, Primary Drying, and Secondary Drying. Commencing with the Freezing phase, the material is subjected to low temperatures, prompting water content to solidify. During Primary Drying, the frozen water undergoes sublimation, transitioning directly from solid to gas without passing through the liquid phase. Subsequently, Secondary Drying eliminates any remaining unfrozen water molecules, ensuring structural stability.
Pressure and Temperature: Guardians of the Lyophilization Process
Pressure and Temperature are key determinants in Lyophilization. In the Freezing phase, controlled low temperatures facilitate the solidification of water content. During Primary Drying, reduced pressure enables sublimation, as the lower pressure prevents water from remaining in its liquid state. In conjunction with controlled Temperature, Pressure governs the transition of water from solid to gas, bypassing the liquid phase, thus preserving the material’s structure.
Preservation of Structure and Quality: Lyophilization’s Artistry
One of the most remarkable aspects of Lyophilization lies in its ability to preserve the Structure and Quality of materials. By removing moisture through sublimation, the original structure is upheld, preventing collapse or distortion. Furthermore, the removal of water mitigates the risk of microbial growth and chemical reactions, thereby enhancing the material’s quality and prolonging its shelf life.
Ensuring Success: Precision and Expertise in Lyophilization
Achieving optimal results in Lyophilization demands precision and expertise. The meticulous control of Pressure and Temperature, coupled with a profound understanding of the material’s characteristics, ensures successful preservation. Moreover, the use of Lyoprotectants, compounds that shield materials from potential damage, contributes to maintaining the material’s integrity during the process.
Mastering Lyophilization: From Lab to Industrial Freeze Drying Lyophilizer
In the forefront of groundbreaking scientific exploration and advancements in the pharmaceutical industry, the Lyophilizer, also referred to as the Freeze-drying machine, reigns supreme. The Vacuum freeze dryer, a technological marvel, has redefined the realm of preservation, particularly in the sphere of Pharmaceutical freeze drying. From Lab lyophilization to the expanse of Industrial freeze drying, its influence extends far and wide.
Delving into the Essence: The Unveiling of Lyophilization
Imagine a world where an array of Freeze-dried products, spanning from delicate Freeze-dried bacteria to vibrant Freeze-dried fruit, owe their existence to the ingenious Lyophilization process. This intricate technique, often intertwined with various Lyophilization techniques, revolves around the extraction of moisture from substances while meticulously maintaining their inherent composition and characteristics.
Unveiling the Lyophilization Technology: A Profound Dive
At the core of this preservation revolution lies the technology of the Freeze dryer. The Lyophilization cycle, anchored by the Vacuum drying method, accomplishes preservation through intricately orchestrated Freeze-drying cycles. This process is further fortified by the incorporation of Lyoprotectants, safeguarding the materials undergoing Freeze drying from potential harm.
A Comprehensive Guide to the Lyophilization Process: Unveiling Each Step
Lyophilization, a process synonymous with freeze-drying, involves a series of intricate steps that result in effective preservation. This article provides a step-by-step breakdown of the Lyophilization process, encompassing Freezing and Formation of Ice Crystals, Sublimation and Removal of Ice, and culminating in Desorption and Final Drying.
Step 1: Freezing and Formation of Ice Crystals
The Lyophilization journey commences with the Freezing phase. During this stage, the material to be preserved is subjected to controlled low temperatures. These conditions prompt the water content within the material to solidify, giving rise to the formation of ice crystals. This preliminary step is crucial as it preps the material for subsequent phases of the process.
Step 2: Sublimation and Removal of Ice
Following freezing, the process seamlessly transitions into the Sublimation phase. In this stage, the frozen ice undergoes sublimation—transitioning directly from a solid state to gas. Remarkably, the ice skips the liquid phase altogether. This occurs due to the vacuum environment maintained within the Lyophilization chamber. As the pressure lowers, the ice particles transform into vapor, leaving behind a material with reduced moisture content.
Step 3: Desorption and Final Drying
The journey culminates in the Desorption and Final Drying phase. At this juncture, the material undergoes thorough desorption, ensuring any remaining unfrozen water molecules are expelled. This meticulous process serves to eradicate the last traces of moisture. The end result is a product with significantly reduced water content, preserving the material’s structure and quality.
Preservation Perfected: The Essence of Lyophilization
The Lyophilization process is marked by its ability to preserve materials in their original form while removing excess moisture. This preservation method is of paramount importance in diverse sectors, ranging from pharmaceuticals to culinary arts, where maintaining the material’s inherent characteristics is critical.
Scientific Precision and Application
Lyophilization requires scientific precision and expertise to achieve optimal results. Parameters such as pressure, temperature, and freeze-drying cycles are carefully monitored to ensure successful preservation. The use of advanced technologies and understanding of the material’s properties play a pivotal role in executing each step effectively.
A Glimpse into the Future of Lyophilization
As technology continues to evolve, so does the Lyophilization process. Emerging trends focus on refining the efficiency of each step, reducing processing times, and enhancing the overall preservation quality. The intersection of innovative techniques, such as the integration of nanotechnology and improved sensing mechanisms, holds the promise of shaping the future of Lyophilization.
In Conclusion: Mastering the Lyophilization Process
The step-by-step journey of Lyophilization—from Freezing and Formation of Ice Crystals, to Sublimation and Removal of Ice, and Desorption and Final Drying—reflects an intricate dance of science and preservation. This process’s ability to delicately extract moisture while upholding material structure solidifies its significance in scientific research, pharmaceuticals, and beyond.
Applications Spanning Industries: Lyophilizer’s Vast Reach
The science of Lyophilization finds applications across diverse industries. From Pharmaceutical freeze drying, preserving sensitive drugs and vaccines, to Culinary freeze-drying techniques, revolutionizing gastronomy, the science plays an essential role. Additionally, Biotechnology and Material Science utilize Lyophilization to preserve biomaterials and delicate structures for further research and development.
Applications of Lyophilizer in the Realms of Pharmaceuticals and Biotechnology
The zenith of Pharmaceutical freeze drying is witnessed in the biotechnology sector through Lyophilization in biotechnology. This technique offers the preservation of essential Freeze-dried vaccines, upholding their effectiveness over time. Moreover, the Shelf freeze dryer employed in laboratories caters to an array of Lyophilization applications, spanning from drug development to advanced medical research.
Beyond Pharmaceuticals: Unveiling the Marvels of Freeze-Dried Cuisine
The far-reaching capabilities of Lyophilization extend beyond laboratories to the culinary realm. The end product of this intricate process, namely Freeze-dried food, has led to the creation of an array of delightful and enduring Freeze-dried powders. These innovative Freeze-dried products have not only revolutionized adventurous dining but have also found their place in the realm of artistic culinary presentations.
Ensuring Quality Control and Assurance of Lyophilizers: Monitoring Parameters and Preventing Degradation
In the realm of Lyophilization, where precision meets preservation, the significance of Quality Control and Assurance cannot be overstated. This article delves into the meticulous art of Monitoring Critical Parameters and Preventing Contamination and Degradation to ensure the integrity of the Lyophilizer’s outcomes.
Step 1: Monitoring Critical Parameters
Maintaining stringent control over critical parameters is fundamental in Lyophilization. Temperature, Pressure, and Time are among the pivotal factors that directly influence the outcome. Accurate temperature control during the Freezing phase ensures uniform ice crystal formation, while precise Pressure control facilitates proper sublimation and removal of ice. The duration of each phase, monitored with precision, contributes to the overall success of the process.
Step 2: Preventing Contamination and Degradation
Contamination and degradation are two adversaries that must be vigilantly guarded against. The sterile environment within the Lyophilization chamber is paramount in preventing microbial contamination. The hermetic sealing of the material during processing is equally crucial to maintain the material’s purity. Additionally, the presence of oxygen and other reactive agents can lead to degradation of sensitive materials. Preventive measures, such as the use of appropriate vials and caps, shield the material from undesired interactions.
Expert Oversight: The Role of Qualified Personnel
Quality Control and Assurance in Lyophilization require the expertise of qualified personnel. Professionals skilled in understanding the interplay of parameters, adept in the interpretation of results, and capable of swift corrective action are instrumental in maintaining the highest standards. Their vigilance ensures that the Lyophilization process yields consistent and reliable outcomes.
Validation and Documentation: Bolstering Assurance
Validation and comprehensive documentation further bolster the Assurance of the Lyophilization process. Extensive data collection, analysis, and verification substantiate the effectiveness of the process. Validation protocols ensure that each Lyophilization cycle adheres to predetermined standards, guaranteeing the repeatability of results and compliance with industry regulations.
Cutting-Edge Technology: Elevating Quality Assurance
Advancements in technology have paved the way for sophisticated monitoring and control systems. These systems, equipped with real-time data tracking and automation, enhance the precision of Lyophilization processes. Sensors that monitor temperature, pressure, and vacuum levels provide immediate insights, enabling prompt adjustments and interventions if necessary.
Future Trends in Quality Control: A Glimpse Ahead
As Lyophilization technology advances, Quality Control and Assurance measures are poised to evolve as well. Emerging trends include the integration of artificial intelligence and machine learning algorithms to predict and prevent process deviations. Such innovations promise to further elevate the reliability and precision of the Lyophilization process.
In Conclusion: Mastering Quality Control and Assurance
Quality Control and Assurance form the bedrock of successful Lyophilization endeavors. By meticulously Monitoring Critical Parameters and Preventing Contamination and Degradation, the integrity of the process is upheld. With the collaboration of skilled personnel and the integration of cutting-edge technology, the Lyophilization process’s future shines bright, ensuring consistent and reliable preservation outcomes.
From Lab to Industry: The Vast Influence of Lyophilization
The journey from Lab lyophilization to Industrial freeze drying signifies a significant progression. The adaptability of Freeze drying equipment is evident in its capacity to cater to an array of diverse Freeze drying solutions. This technological prowess has empowered the emergence of Lyophilization services, effectively bridging the gap between scientific research and practical applications.
Lyophilization: A Glance at Today and Tomorrow
As technology continues to evolve, so does the landscape of Lyophilization technology. The realm of Industrial freeze drying is witnessing the integration of cutting-edge Vacuum freeze dryers, distinctly different from their Laboratory-scale lyophilizer counterparts. This progression holds the potential to redefine our approach to preservation, transcending industry boundaries and disciplinary confines.
In Conclusion: The Everlasting Legacy of the Lyophilizer
In the dynamic interplay of scientific progress and culinary innovation, the Lyophilizer remains an unwavering force. From its pivotal role in Pharmaceutical freeze drying to the preservation of intricate culinary creations, this Freeze-drying machine has indelibly transformed the preservation landscape. As it continues to evolve, the legacy of the Lyophilizer is poised to transcend limitations and explore new horizons.
Frequently Asked Questions
1. What is the primary function of a Lyophilizer?
The Lyophilizer, also known as the Freeze-drying machine, primarily serves to extract moisture from substances while preserving their inherent structure and characteristics.
2. What are the key phases of the Freeze-Drying Process?
Freezing, Primary Drying, and Secondary Drying.
3. How do Pressure and Temperature influence Lyophilization?
Pressure and Temperature play a pivotal role in facilitating sublimation, transitioning water from solid to gas, thus preserving the material’s structure.
4. How does Lyophilization contribute to the pharmaceutical industry?
Lyophilization plays a pivotal role in Pharmaceutical freeze drying, enabling the preservation of sensitive substances like Freeze-dried vaccines.
5. Can Lyophilization be employed in the culinary world?
Indeed, Lyophilization has ventured into the culinary domain, leading to the creation of enduring Freeze-dried food products.
6. What are some emerging trends in Lyophilization technology?
The progression from Laboratory-scale lyophilizers to advanced Vacuum freeze dryers for Industrial freeze drying signifies a promising trend in Lyophilization technology.
7. How does Lyophilization benefit various industries?
Lyophilization has a universal appeal, contributing to fields as diverse as pharmaceuticals, biotechnology, and gastronomy, by offering advanced preservation solutions.
View more about Freeze Drying on Wikipedia