In the realm of cannabis and botanical extraction, closed-loop extractors have evolved into indispensable tools for crafting top-notch concentrates. These advanced extraction systems empower manufacturers to efficiently extract essential oils, terpenes, and other valuable compounds from plant material.
In the world of modern extraction techniques, closed-loop extractors have emerged as essential tools for obtaining high-quality concentrates from botanical materials. Whether you’re a seasoned extractor or just getting started, choosing the right closed-loop extractor can significantly impact your final product’s quality and yield. In this comprehensive guide, we’ll walk you through the crucial factors to consider when selecting the ideal closed-loop extractor for your needs.
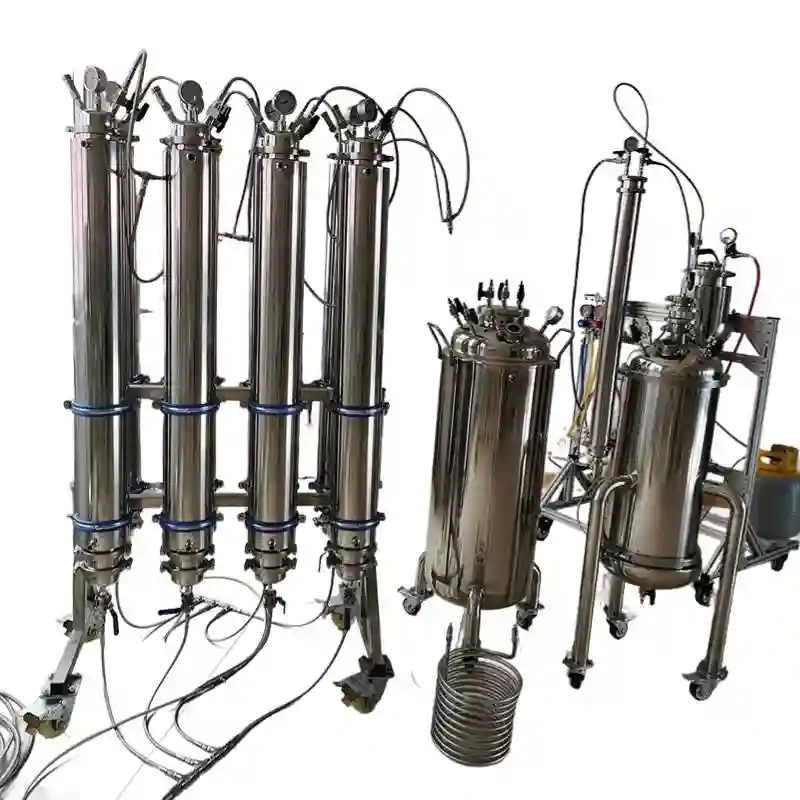
Closed loop extractors have brought about a revolutionary transformation in the art of obtaining concentrated extracts from plant materials. Unlike the outdated open blasting techniques, closed loop extraction systems are engineered to be safer, highly efficient, and ecologically sustainable. Whether your focus is on extracting essential oils, crafting concentrates for the cannabis industry, or formulating botanical extracts for perfumery, the paramount decision is selecting the most fitting closed loop extractor.
Understanding Closed Loop Extractors
What Is a Closed Loop Extractor and How Does It Work?
Closed-loop extractors are advanced machines designed to utilize solvents for extracting compounds from plant materials. The distinctive feature of the “closed loop” design ensures a constant recycling of solvents, leading to reduced waste and enhanced operational efficiency. As a result, this method produces cleaner, more refined extracts that are highly sought after for their potency and unique aroma.
A closed-loop extractor is a specialized apparatus employed in the extraction process of essential oils, concentrates, or other valuable compounds from plant sources like herbs and botanicals. It finds widespread use in industries such as cannabis and herbal extraction, where it enables the efficient and secure isolation of specific compounds.
The “closed-loop” aspect of the extractor refers to its sealed system, which minimizes the exposure of the operator and the environment to potentially hazardous solvents used in the extraction process. Here’s how a closed-loop extractor generally works:
- Loading: The plant material, often dried and ground, is loaded into a chamber within the closed-loop extractor.
- Solvent Injection: A solvent, usually a liquefied gas like butane or propane, is injected into the chamber containing the plant material. The solvent acts as a medium to dissolve and carry the desired compounds from the plant material.
- Extraction: The solvent interacts with the plant material, dissolving the target compounds, such as essential oils or cannabinoids. This forms a solution containing the desired compounds and other plant components.
- Filtration: The solution is then passed through a series of filters to separate the extracted compound-laden solvent from the remaining plant material. These filters help remove any solid particles and impurities.
- Recovery: The filtered solution is then transferred to another part of the closed-loop system, often referred to as the recovery vessel. In this vessel, the solvent is carefully and precisely evaporated or purged, leaving behind a concentrated form of the desired compounds.
- Condensation and Recycling: The evaporated solvent is condensed back into liquid form through cooling methods, and it can be recycled for future extractions. This closed-loop process minimizes solvent waste and reduces environmental impact.
- Collection: The final extracted compound, now in a concentrated form, is collected and stored for further processing or use in various applications.
It’s important to note that closed-loop extractors are designed with safety as a top priority. The closed system prevents the release of solvents into the environment, reducing the risk of exposure to harmful gases. Additionally, closed-loop extractors often come equipped with safety features such as pressure relief valves and monitoring systems to prevent over-pressurization and ensure a controlled extraction process.
Overall, closed-loop extractors are widely used in industries that require efficient and controlled extraction of valuable compounds from plant materials, while prioritizing safety and environmental responsibility.
Benefits of Closed Loop Extraction
Closed loop extraction offers a multitude of advantages over the traditional open blasting methods. These include:
- Higher Extraction Efficiency: Closed loop systems allow meticulous control over extraction parameters, yielding increased output and consistent outcomes.
- Enhanced Safety: The closed loop design substantially mitigates the risk of solvent exposure and significantly reduces the likelihood of accidents during the extraction process.
- Improved Quality: The closed loop process conserves the delicate aromas and flavors of plant materials, resulting in extracts of superior quality.
- Environmental Friendliness: Closed loop extractors are meticulously engineered to be ecologically conscious, recycling solvents and minimizing overall waste production.
Factors to Consider When Selecting a Closed Loop Extractor
When making the pivotal choice of a closed loop extractor, several crucial factors demand consideration:
1. Types of Solvent
Different solvents possess distinct extraction properties and safety considerations. Noteworthy solvents include butane, propane, ethanol, and CO2. The selection of the solvent hinges upon the desired final product and regulatory prerequisites.
2. Extraction Scale
The scale of your extraction operation merits careful deliberation. Closed loop extractors come in a range of sizes, from small-scale units catering to personal use, to larger, commercial-grade systems.
3. Material Compatibility
Ensuring alignment between your chosen extractor and the specific plant material you’re working with is paramount. Diverse materials may necessitate particular extraction methods and parameters.
4. Automation Level
Extractors may offer automated features streamlining the extraction process, or they may require a more hands-on approach. Opt for a system that harmonizes with your workflow preferences and proficiency.
5. Safety Features
Prioritizing safety features like pressure relief valves, automatic shut-off mechanisms, and effective ventilation is pivotal to minimizing risks during operation.
6. Maintenance and Durability
Regular maintenance is pivotal for the longevity of your extractor. Seek systems that facilitate easy cleaning and upkeep, equipped with durable components capable of enduring frequent usage.
7. Cost Considerations
While quality comes at a price, it’s imperative to find an extractor that strikes a balance between performance and cost-effectiveness.
8. Reputation and Support
Thoroughly research the manufacturer’s reputation and assess their customer support services. Reliable technical support proves invaluable in the event of operational hitches.
9. User Reviews and Recommendations
Consult user reviews and solicit advice from industry peers for real-world insights into the performance of various extractors.
However, the most important thing in choosing ideal closed loop extractor is choosing the right size.
Factors to Consider When Choosing Extractor Size
Type of Plant Material
The type of plant material you intend to extract plays a crucial role in determining the appropriate extractor size. Different plants have varying levels of essential oil content, which affects the overall extraction yield. Some plants may require a larger extractor to accommodate their higher oil content, while others may work well with a smaller system.
Extraction Scale
Are you a small-scale artisanal extractor or a large-scale commercial operation? The scale of your extraction business heavily influences the choice of extractor size. Small-scale extractors may find a compact system sufficient, whereas larger operations demand higher-capacity extractors to meet production quotas.
Production Goals
Before choosing an extractor size, clearly define your production goals. Consider factors such as daily output and projected growth. Having a clear understanding of your production needs will help you select a size that aligns with your business objectives.
Solvent Usage
The amount of solvent you plan to use during extraction is another vital consideration. Some closed loop extractors are designed to handle larger solvent volumes, making them suitable for high-throughput operations. Conversely, smaller systems may be more efficient for those using minimal solvent.
Space and Budget Constraints
Your available space and budget are practical constraints that must be taken into account. Larger extractors may require a more spacious facility, while smaller ones are suitable for limited spaces. Moreover, your budget will influence the range of extractor sizes you can realistically consider.
Calculating the Right Extractor Size
To determine the optimal closed loop extractor size, a combination of factors must be considered. One common approach is to calculate the solvent-to-material ratio, which helps identify the most efficient extractor size for your specific plant material and production goals. Consulting with extraction experts can provide valuable insights into this calculation.
Benefits of Choosing the Right Extractor Size
Maximizing Efficiency
Selecting the right extractor size ensures optimal efficiency during the extraction process. Overloading a small extractor can lead to subpar extraction yields, while using a large system for minimal amounts of material is inefficient.
Conserving Resources
An appropriately sized extractor helps conserve resources such as solvent and energy. Operating a system that matches your production needs prevents unnecessary waste and lowers operational costs.
Maintaining Product Quality
Proper extractor sizing contributes to consistent product quality. Under-sizing or over-sizing can lead to uneven extraction, impacting the flavor, aroma, and overall potency of your extracts.
Steps to Ensure Safe and Effective Extraction
- Research and Education: Gain a thorough understanding of closed loop extraction principles and safety protocols.
- Choose the Right Solvent: Select a solvent suitable for your plant material and extraction goals.
- Optimize Operating Conditions: Adjust parameters such as temperature and pressure to achieve optimal extraction efficiency.
- Regular Maintenance: Perform routine maintenance to ensure the longevity and performance of your extractor.
- Quality Control Testing: Implement quality control measures to monitor the consistency and potency of your extracts.
Professional Tips for Extractor Sizing
- Consult with experienced extraction professionals to determine the best extractor size for your needs.
- Consider modular extractor systems that allow for scalability as your business grows.
- Factor in potential future expansion when deciding on an extractor size.
Maintenance and Upgrades
Regular maintenance is essential to keep your closed loop extractor operating smoothly. Additionally, stay informed about technological advancements and consider upgrading your system to incorporate the latest innovations, improving both efficiency and safety.
Common Mistakes to Avoid
- Neglecting proper training and education on closed loop extraction techniques.
- Underestimating the importance of extractor size in overall extraction efficiency.
- Overlooking safety protocols and regulations in the pursuit of higher yields.
The Future of Closed Loop Extraction
As extraction technology continues to evolve, closed loop extractors are expected to become more efficient, environmentally friendly, and user-friendly. Innovations in solvent recovery, automation, and precision control will shape the future of closed loop extraction.
Exploring Extraction Methods
Supercritical CO2 Extraction:
Supercritical CO2 extraction is a method that utilizes carbon dioxide in its supercritical state as a solvent to extract essential compounds from various materials, such as plant matter. In this state, CO2 behaves both like a gas and a liquid, making it an effective solvent for extracting compounds like oils, flavors, and fragrances. The process involves pressurizing CO2 to a supercritical state and passing it through the plant material. When the pressure is released, the CO2 returns to its gaseous state, leaving behind the extracted compounds. This method is preferred for its ability to selectively extract specific compounds, low environmental impact, and lack of residue in the final product.
Hydrocarbon Extraction:
Hydrocarbon extraction involves using hydrocarbon solvents, such as butane or propane, to separate essential oils and other compounds from plant materials. The process typically involves soaking the material in the hydrocarbon solvent, which dissolves the desired compounds. The solvent is then evaporated to leave behind a concentrated extract. However, this method can be potentially dangerous due to the flammable nature of hydrocarbons, and proper safety measures must be taken to prevent explosions or fires. Despite the risks, hydrocarbon extraction is popular in the cannabis industry for its efficiency in preserving terpenes and cannabinoids.
Alcohol Extraction:
Alcohol extraction, also known as ethanol extraction, is a process that uses ethanol (or other types of alcohol) as a solvent to extract compounds from botanical materials. The plant material is soaked in alcohol, which dissolves the desired compounds. The alcohol is then evaporated, leaving behind the extracted substance. This method is relatively safe and is commonly used for making tinctures, herbal extracts, and concentrates. It also preserves a wide range of compounds from the plant material, including cannabinoids, terpenes, and flavonoids. However, careful control of temperature and extraction time is required to avoid extracting unwanted compounds and chlorophyll, which can affect the taste and quality of the final product.
Each of these extraction methods has its own advantages and considerations, and their suitability depends on the specific application and the desired properties of the final product. It’s important to carefully choose the extraction method that aligns with your goals and safety requirements.
Conclusion
Choosing the ideal closed loop extractor is a critical decision that can significantly impact the quality and efficiency of your extraction process. By carefully considering factors such as solvent type, extraction scale, safety features, and maintenance requirements, you can make an informed choice that aligns with your extraction goals and operational needs.
FAQs (Frequently Asked Questions)
- Q: What is the difference between closed loop extraction and open blasting? A: Closed loop extraction is a safer and more controlled method that recycles solvents, while open blasting is a riskier process that involves blasting solvents over plant material.
- Q: Can I use any solvent in a closed loop extractor? A: No, the choice of solvent should be based on the desired end product and safety considerations.
- Q: Are closed loop extractors suitable for small-scale operations? A: Yes, there are closed loop extractors available in various sizes to accommodate both personal and commercial use.
- Q: How often should I perform maintenance on my closed loop extractor? A: Regular maintenance should be performed according to the manufacturer’s recommendations to ensure optimal performance and longevity.
- Q: Where can I find reliable technical support for my closed loop extractor? A: Many reputable manufacturers offer customer support services to assist with troubleshooting and technical issues.
View more about Extraction on Wikipedia