In the realm of industrial drying equipment, one technology stands out for its efficiency and versatility: spray dryer technology. This innovative process, also known as atomization, has transformed powder production across various industries through its advanced evaporation techniques and optimized drying chamber design. From handling heat-sensitive materials to achieving precise product moisture control, spray drying technology has become a cornerstone in modern manufacturing.
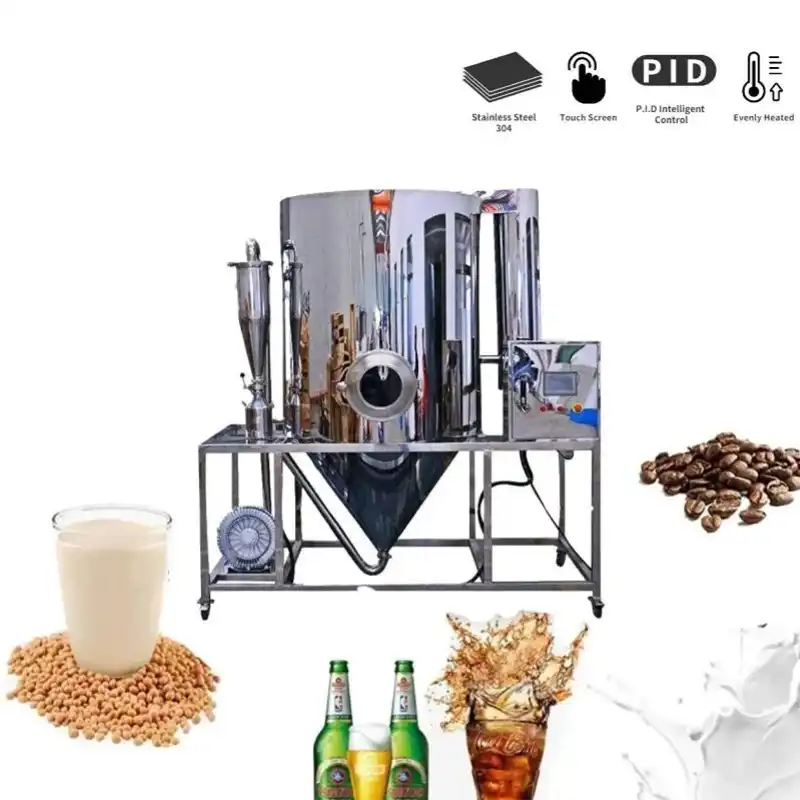
Unveiling the Power of Spray Drying
Decoding Spray Drying
Spray drying is a widely used process in various industries to transform liquid substances, often in the form of solutions, suspensions, or emulsions, into dry powders. It’s a method of choice for producing powdered products like food ingredients, pharmaceuticals, ceramics, and more. It encompasses the atomization of a liquid feed into a heated drying medium, resulting in droplets that lose moisture as they traverse, ultimately forming fine particles.
The Process Unraveled
The initial step involves preheating the liquid, which is subsequently introduced into the drying chamber. Concurrently, hot gas, often air, is introduced, prompting the evaporation of liquid content and the formation of dry particles.
key principles:
Atomization: The liquid feed material is atomized into tiny droplets using a nozzle or other atomization methods. This is typically done to increase the surface area of the liquid, allowing for faster evaporation.
Drying Chamber: The atomized droplets are introduced into a drying chamber. This chamber is usually a large, cylindrical structure where hot air is introduced. The hot air serves two main purposes: it provides the heat necessary for evaporation, and it helps carry away the moisture as it evaporates from the droplets.
Heat Transfer: The hot air in the drying chamber comes into direct contact with the atomized droplets. Heat is transferred from the hot air to the droplets, causing the liquid within the droplets to evaporate. The droplets progressively lose moisture and shrink in size.
Moisture Evaporation: As the liquid evaporates, the solid components within the droplets become more concentrated. This concentration can sometimes lead to the formation of a shell or outer layer around the droplet, preventing the inner moisture from escaping quickly. This is why optimizing the drying conditions is crucial to achieve desired product properties.
Powder Formation: Once the moisture content within the droplets reduces significantly, what remains are solid particles or particles with a thin layer of concentrated material. These particles are then separated from the drying air using cyclones, bag filters, or other separation methods.
Product Collection: The dried particles, now in the form of a fine powder, are collected from the separation equipment. Depending on the application, additional steps like sieving, milling, or agglomeration might be required to achieve the desired particle size distribution and product characteristics.
Key Factors and Considerations:
Feed Material: The properties of the liquid feed material (such as viscosity, concentration, and surface tension) significantly impact the atomization and drying process. Different materials require specific equipment and conditions.
Temperature Control: The temperature of the drying air is crucial for efficient moisture removal. Too high a temperature could lead to product degradation or unwanted reactions, while too low a temperature might result in insufficient drying.
Airflow and Residence Time: Proper airflow rates and residence time (the duration that particles spend in the drying chamber) are important for achieving complete drying and preventing overheating.
Particle Size and Quality: The desired particle size distribution and product quality influence the process parameters and equipment selection.
Equipment Design: Spray dryers come in various designs, such as rotary atomizers, nozzle atomizers, and fluidized bed dryers. The choice of equipment depends on the feed material and the desired product properties.
In summary, spray drying is a versatile technique that allows liquid materials to be converted into dry powders through atomization, heat transfer, and moisture evaporation. It’s widely used across industries to produce a range of powdered products with specific characteristics.
Applications in Diverse Industries
Exploring food industry applications of spray dryers
Spray drying is a versatile technique widely employed in the food industry to transform liquid or semi-liquid substances into powdered forms. This process involves atomizing a liquid feed into small droplets, which are then exposed to a stream of hot air in a drying chamber. The rapid evaporation of moisture results in the formation of fine particles that can be easily collected as dry powder. This technique offers several benefits for various food applications:
Dairy Products: Spray drying is commonly used to produce powdered milk, creamers, and dairy-based ingredients like whey and casein. The process helps extend the shelf life of these products while preserving their nutritional value and flavor.
Beverages: Instant coffee, tea extracts, and fruit juices can be spray-dried to create soluble powders that quickly dissolve when mixed with water. This enhances convenience for consumers while maintaining the beverage’s original taste and aroma.
Flavors and Aromas: Spray drying is also employed to create encapsulated flavors and aromas. This technique involves coating the volatile compounds responsible for taste and scent with a protective layer, preserving their potency until the powder is rehydrated during consumption.
Food Additives: Many food additives, such as emulsifiers, stabilizers, and colorants, are produced using spray drying. This ensures uniform distribution in the final product and improved handling during manufacturing.
Baby Food: Nutrient-rich baby formulas and cereals can be produced through spray drying, offering a convenient and safe way to provide essential nutrition to infants.
Spices and Seasonings: Spray-dried spice extracts and seasoning blends can enhance the flavor profile of various dishes, while their powdered form ensures easy incorporation into recipes.
Functional Ingredients: Food ingredients with functional properties, such as dietary fibers and protein supplements, can be spray-dried to create concentrated powders that can be seamlessly integrated into various food products.
Pharmaceutical applications: enhancing drug formulation through spray drying
Spray drying has found significant applications in the pharmaceutical industry, particularly in the enhancement of drug formulation and delivery. The technique offers precise control over particle size, morphology, and drug encapsulation, leading to improved solubility, bioavailability, and stability of pharmaceutical compounds:
Enhanced Solubility: Many drug compounds suffer from poor water solubility, which can hinder their absorption and therapeutic efficacy. Spray drying can convert these poorly soluble drugs into amorphous or nanocrystalline forms, significantly improving their solubility and dissolution rates.
Particle Engineering: By controlling the size and shape of particles produced through spray drying, pharmaceutical companies can tailor drug delivery systems to specific requirements. This includes designing particles for sustained release, targeted delivery, or inhalation-based therapies.
Stability Improvement: Spray drying can protect drugs from degradation caused by environmental factors, such as light, moisture, and heat. By encapsulating drugs within a protective matrix, their stability can be significantly enhanced.
Taste-Masking: Pediatric and geriatric patients, as well as individuals with difficulty swallowing, often struggle with bitter-tasting medications. Spray drying can be utilized to mask the taste of drugs by encapsulating them within taste-masking excipients.
Inhalable Formulations: For respiratory therapies, spray drying enables the creation of fine particles suitable for inhalation. This allows drugs to be directly delivered to the lungs, offering a faster onset of action and reduced systemic side effects.
Biologics and Vaccines: Spray drying has been explored for preserving the stability of biologic drugs and vaccine components, facilitating their storage and distribution without the need for extreme cold-chain conditions.
Personalized Medicine: The flexibility of spray drying makes it conducive to the development of personalized drug formulations, allowing the adjustment of dosages and delivery mechanisms based on individual patient needs.
The applications of spray drying in both the food industry and pharmaceutical sector showcase its versatility and potential to revolutionize various processes, from food production to drug development.
The Merits of High-Performance Spray Dryers
Acceleration of Production Velocity
Conventional drying methodologies can be laboriously time-intensive. High-performance spray dryers dramatically curtail drying durations, equipping manufacturers to meet stringent production timelines.
Elevation of Product Uniformity
Homogeneous particle sizes carry paramount importance, especially in sectors like pharmaceuticals. High-performance spray dryers guarantee consistent particle dimensions, contributing to uniform reconstitution and dissolution rates.
Eco-Friendly Energy Enhancements
Modern spray dryers are meticulously designed to uphold energy efficiency, leading to reduced operational expenses and a diminished environmental footprint. This aligns seamlessly with the prevailing emphasis on sustainability.
The Vitality of High-Performance Solutions
Meeting Escalating Efficiency Needs
Driven by the rapid pace of industries, the demand for swifter and more efficient production processes has surged. High-performance spray dryers rise to this challenge by significantly curtailing drying times.
Preserving Pristine Quality
Maintaining the integrity of the final product has perennially posed a concern. High-performance solutions confront this challenge by meticulously overseeing the drying process, thereby averting the degradation of delicate materials.
Pioneering Innovations in Spray Drying
Revolutionary Nozzle Designs
Nozzles stand as a pivotal factor in the realm of spray drying, wielding influence over droplet size and distribution. High-performance nozzles facilitate enhanced atomization, fostering uniform drying and consistent particle dimensions.
Integrated Drying Systems
Modern spray dryers are fortified with integrated systems that confer meticulous control over parameters such as temperature, airflow, and feed rates. This orchestration ensures ideal drying conditions and impeccable product quality.
Real-time Monitoring
High-performance spray dryers come equipped with advanced monitoring systems, enabling operators to track variables in real time. This adaptability allows for instantaneous adjustments, culminating in heightened process control and efficiency.
Environmental Impact and Sustainability
Assessing the environmental footprint of spray drying processes:
Spray drying is a common industrial process used to transform liquid solutions or suspensions into dry powders or granules. While it offers numerous advantages in terms of product preservation and production efficiency, it can have a notable environmental footprint due to energy consumption, emissions, and resource usage. Here’s how you might assess its environmental impact:
Energy Consumption: Calculate the energy consumption of the spray drying process, including heating the drying air, operating the atomization system, and powering the equipment. This can be assessed in terms of kilowatt-hours (kWh) or other relevant units.
Emissions: Quantify emissions from the process, including greenhouse gases (such as CO2), volatile organic compounds (VOCs), and particulate matter. These emissions can contribute to air pollution and climate change.
Water Usage: Evaluate the amount of water used for the process, considering both the liquid feed and the water required for cooling and cleaning. Assess the source of water and potential impact on local water resources.
Raw Material Inputs: Analyze the resources required for feedstock preparation, such as the energy and materials needed to produce the liquid solution or suspension.
Waste Generation: Calculate the amount of waste generated during the process, including any byproducts or waste streams that need to be treated or disposed of.
Life Cycle Assessment (LCA): Conduct a comprehensive life cycle assessment to analyze the environmental impact from raw material extraction to product disposal. This will provide a holistic view of the process’s footprint.
Strategies for making spray drying more eco-friendly:
To make spray drying processes more eco-friendly and sustainable, several strategies can be implemented:
Energy Efficiency: Implement energy-saving technologies, such as heat recovery systems, to minimize energy consumption during drying. Use renewable energy sources, like solar or wind power, to reduce the carbon footprint.
Optimized Operation: Fine-tune operating parameters like temperature, air velocity, and feed concentration to achieve better drying efficiency, which can lead to shorter drying times and lower energy consumption.
Advanced Atomization Techniques: Employ advanced atomization methods, such as pressure-swirl or ultrasonic atomization, which can lead to better droplet control and reduced energy requirements.
Closed-Loop Systems: Implement closed-loop systems that recirculate drying air and process fluids, reducing water consumption and minimizing emissions.
Alternative Feedstocks: Explore the use of alternative, sustainable feedstocks that have a lower environmental impact. This could include waste byproducts from other industries or agricultural residues.
Waste Minimization: Implement processes that minimize waste generation. Consider technologies like encapsulation to reduce the loss of volatile compounds during drying.
Cleaner Emission Control: Install effective emission control technologies, such as scrubbers or catalytic converters, to mitigate air pollutants and VOC emissions.
Material Recovery: Explore opportunities for recovering valuable byproducts or compounds from the process waste streams, reducing waste and potentially generating additional revenue.
Lifecycle Design: Consider the entire lifecycle of the product and process when designing equipment and making decisions. Optimize for reusability, recyclability, and reduced environmental impact at every stage.
Certifications and Standards: Adhere to environmental certifications and standards that guide sustainable manufacturing practices, such as ISO 14001 or LEED.
Continuous Improvement: Regularly monitor and assess the environmental performance of the spray drying process, seeking continuous improvement through data analysis and innovation.
By combining these strategies and continuously innovating, spray drying processes can be transformed into more eco-friendly and sustainable operations, reducing their environmental footprint while maintaining production efficiency.
Frequently Asked Questions
Are high-performance spray dryers suitable for small-scale businesses?
Indeed, high-performance spray dryers can be meticulously tailored to various production scales, rendering them equally applicable to both small-scale and large-scale enterprises.
Which industries stand to gain the most from these advancements?
Industries encompassing pharmaceuticals, food production, chemicals, and materials processing are poised to glean substantial benefits from the efficacy and quality enhancements provided by high-performance spray dryers.
Do high-performance spray dryers necessitate specialized maintenance?
Although the maintenance requisites can fluctuate, manufacturers typically furnish comprehensive guidelines and support for the maintenance and servicing of their high-performance spray dryer systems.
In what manner do high-performance spray dryers contribute to sustainability?
These spray dryers effectuate reduced energy consumption, curtailed waste generation, and optimized production procedures, thereby aligning with sustainability objectives and diminishing environmental repercussions.
Where can one access these cutting-edge spray dryer solutions?
Access the latest in high-performance spray dryer solutions at https://labonsale.com/product/spray-drying/.
View more about Spray Drying on Wikipedia