Glass reactors hold a pivotal role in the realm of chemical research and industrial processes. Their significance lies in facilitating experiments, mixing substances, and catalyzing reactions across diverse industries. Delve into this comprehensive guide to unravel the intricate world of glass reactors, from their core concept and operational principles to their manifold applications and benefits.
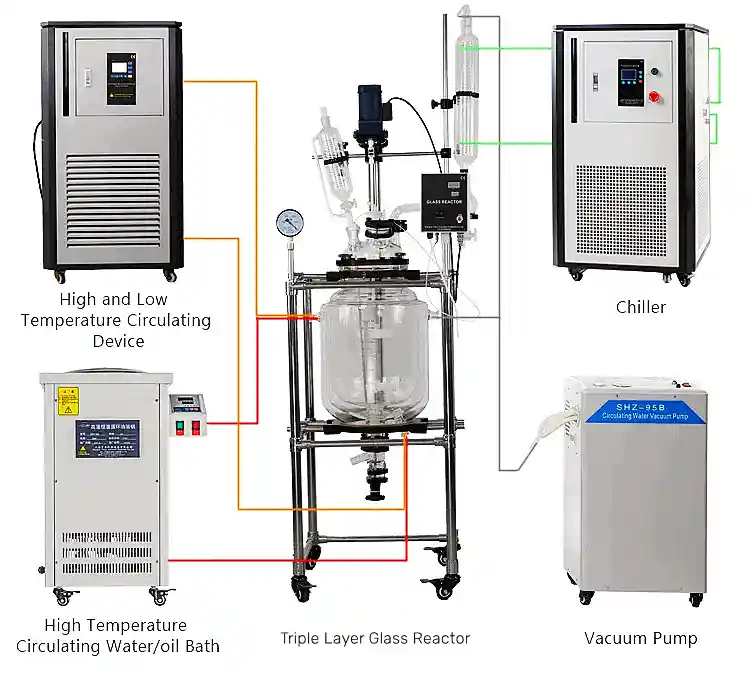
Demystifying Glass Reactors: A Closer Look
A glass reactor, also known as a jacketed reactor or a glass vessel, stands as a vessel constructed from premium borosilicate glass. Its utility extends to laboratories and industries alike, where it becomes the stage for conducting chemical reactions under carefully controlled circumstances. The inherent transparency of glass empowers researchers with the ability to visually monitor these reactions, rendering it a priceless asset in the realms of both research and production.
Components That Power Glass Reactors
A standard-issue glass reactor comprises a repertoire of essential components:
- Glass Vessel: The core body of the reactor, fashioned predominantly from borosilicate glass, is renowned for its remarkable resilience to temperature fluctuations and chemical corrosion.
- Jacket: A dual-layered structure enveloping the glass vessel, housing a heat-transfer medium. This feature orchestrates meticulous temperature control during reactions.
- Stirring System: A motor-driven agitator, the beating heart of the reactor, ensures unfaltering mixing and uniform distribution of reactants within the vessel.
- Ports and Valves: These strategic openings, adorning the reactor’s lid or body, facilitate the introduction of reactants, the extraction of samples, and the surveillance of process variables.
- Condenser: A cooling mechanism that transmutes vapor into liquid form, thereby enabling the recuperation of volatile substances.
- Thermometer and Pressure Gauge: These instruments bear the weight of monitoring temperature and pressure levels ensconced within the reactor.
- Heating/Cooling System: An external entity harmoniously tethered to the jacket, embracing the task of preserving the desired reaction temperature.
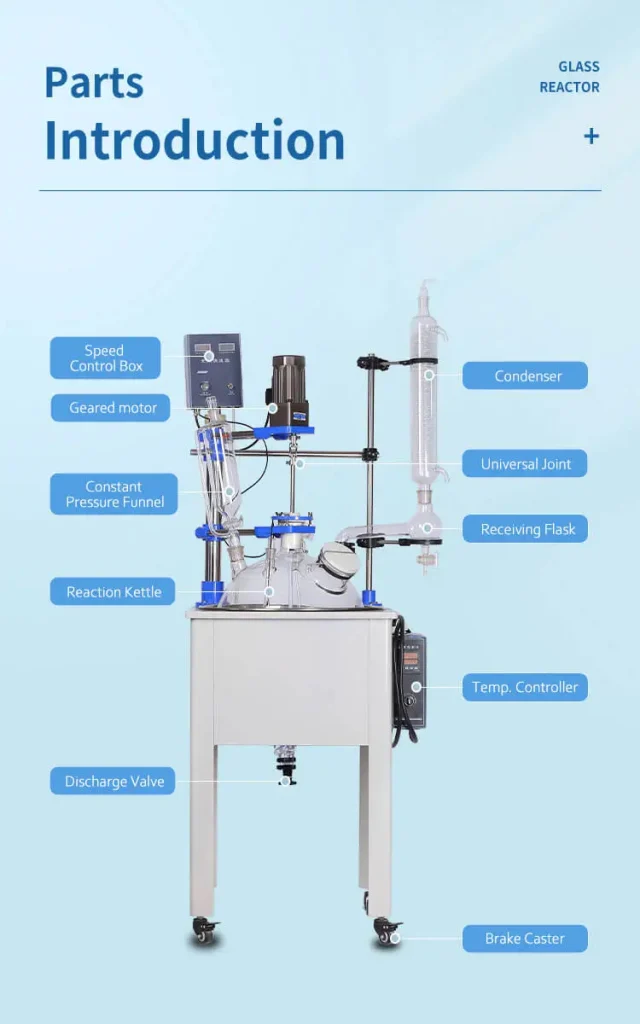
Unraveling the Mechanism: Glass Reactors in Action
Glass reactors operate in alignment with the principles of chemical engineering, orchestrating the introduction of reactants into the vessel, their harmonious mingling, and the orchestration of their reactions within the cocoon of controlled conditions. The cocoon, represented by the jacket enveloping the glass vessel, presides over the art of meticulous temperature manipulation via the circulation of a heat-transfer fluid. The stirring system emerges as the conductor, orchestrating uniform mixing and thereby elevating reaction efficiency.
The initiation of a reaction materializes with the measured introduction of necessary reactants via the designated ports. The stirring system’s indefatigable efforts propel the dance of the reaction. In scenarios demanding a surge of heat, the jacket’s heating system raises temperatures to desired levels. Conversely, the cooling routine unfurls with the circulation of a cooling fluid through the jacket in instances when exothermic reactions generate excess heat.
Variants of Glass Reactors: A Taxonomy
The sphere of glass reactors encompasses a diverse array of variants, meticulously designed for specific applications and reaction circumstances.
Batch Reactors
Embarking as the simplest iteration, batch reactors flourish in a discrete domain, where reactants enter, interact, and then exit once the reaction reaches fruition. Their prowess is showcased in experiments and processes demarcated by defined initiation and cessation points.
Continuous Reactors
A departure from the intermittent rhythm of batch reactors, continuous reactors embrace a ceaseless inflow of reactants. Concurrently, products steadily ebb away. This realm is conducive to large-scale production and the orchestration of processes that thrive on the perpetual supply of reactants.
Plug Flow Reactors (PFR)
Plug flow reactors are designed to ensure that the reactants flow through the reactor in a continuous plug-like manner, without mixing with the already reacted material. They are ideal for reactions requiring precise control over reaction times and conditions.
CSTR (Continuous Stirred Tank Reactors)
CSTRs, firmly entrenched in industrial landscapes, perpetuate a constant stream of reactants, punctuated by seamless mixing via agitation. They emerge as versatile titans, adept at governing a gamut of reactions.
The Pantheon of Glass Reactor Advantages
The zenith of glass reactor utility is underscored by an array of advantages that span myriad applications and industries. These advantages are inexorably intertwined with the unique properties and design of glass reactors:
- Visibility: Glass reactors, veiled in transparency, unfurl an unobstructed view of the entire reaction narrative. Operators partake in the unfolding saga sans having to pry open the vessel. This visual control translates into augmented mastery over reactions, early anomaly detection, and the scope for real-time adaptations.
- Chemical resistance: The commendable resistance of glass to diverse chemicals positions it as an able steward for a pantheon of corrosive and reactive substances. The sanctity of the reaction is preserved, and the specter of cross-contamination dissipates into oblivion.
- Inertness: Glass embraces the moniker of an inert being, steadfastly resisting the urge to react with the majority of chemicals. This unique trait ensures reactions transpire under the banner of desired conditions, unmarred by unintended tangents borne of reactor interaction.
- Easy cleaning and sterilization: Glass reactors gallantly march into the realm of ease of cleaning and sterilization. Each experiment arises from a pristine vessel, scrubbed free of residue from yesteryears. The crucible is particularly pertinent in sectors such as pharmaceuticals, biotechnology, and gastronomy, where contamination’s phantom looms large.
- Thermal resistance: The hallowed precincts of high-quality borosilicate glass resonate with a wide-ranging temperature forbearance. Cryogenic climes and high-temperature odysseys all find solace in its embrace. This versatile panorama summons forth a spectrum of reaction conditions.
- Scalability: Glass reactors, donning various garbs of size, from minuscule laboratory vials to industrial behemoths, beckon researchers to embark on a journey from the realms of experimentation to the sprawling domains of commercial production. The path remains unperturbed, the conditions unaltered.
- Versatility: Glass reactors engage in an intricate dance, donning the mantles of diverse reactions—batch reactions, continuous flow symphonies, and the quintessence of reflux reactions. Their siren call echoes across pharmaceuticals, chemicals, petrochemicals, the culinary stage, and the corridors of academia.
- Safety: Unlike their metallic counterparts, glass reactors eschew the art of producing sparks. A tapestry of safety unfurls, especially for reactive or flammable chemicals. Furthermore, the vessel’s transparency flanks operators, enabling the timely identification of leaks or undue pressure buildups.
- Reduced contamination risk: Glass reactors don the mantle of purity, a feat beyond reach for some metallic cousins. A vital attribute, as pristine reactions dictate terms in pharmaceuticals and the alchemy of fine chemicals.
- Cost-effectiveness: The economic realm finds an ally in glass reactors. A modest entry cost converges with an extended lifespan when nurtured with care, painting a portrait of financial sagacity.
Despite these advantages, glass reactors also have some limitations. They are relatively fragile and may not be suitable for certain high-pressure or high-temperature applications. For extreme conditions, other materials like stainless steel or exotic alloys may be preferred. Additionally, care must be taken to avoid mechanical damage or temperature shocks that could cause fractures in the glass.
Applications Illumined: Glass Reactors at Play
Glass reactors gallivant across a plethora of applications in assorted industries and research fraternities. Their chameleon nature, along with their inherent advantages, sponsors a multitude of scenarios:
- Chemical Synthesis: In the sanctuaries of chemical laboratories and industrial echelons, glass reactors unveil their potency as instruments of chemical synthesis. Organic and inorganic compounds step into the limelight, their reactions orchestrated with precision. Transparency orchestrates real-time optimization, ushering in the reign of reaction conditions and yield.
- Pharmaceutical Industry: Glass reactors secure their throne in the realm of pharmaceuticals, a realm eternally punctuated by research and production. The sanctum hosts the crafting of active pharmaceutical ingredients, intermediates, and drug symphonies. Purity is not mere rhetoric; it is the hallmark of pharmaceutical safety.
- Petrochemical Industry: Petrochemical vistas welcome the glass reactor, finding solace in processes ranging from specialty chemical craftsmanship to the birth of polymers and catalysts. Glass’s resistance unfurls its canvas to welcome the deluge of corrosive companions.
- Food and Beverage Industry: In the culinary haven, glass reactors stand as paragons, where research and development unfurl their wings. Food processing finds its elixir, novel products bask in creation, and the interplay of ingredients dances under the scrutiny of glass’s unwavering gaze.
- Biotechnology and Biochemistry: Biotechnology and biochemistry spin their tales, wherein fermentation, cell culture, enzyme affairs, and protein expositions command the stage. Glass reactors emerge as custodians of transparency, monitoring the crescendos and diminuendos of cell growth and reaction progress.
- Environmental Testing: Environmental quests rally under the glass reactor’s standard. Water and air unveil their secrets, wastewater meets its treatment, and hazardous essences find redemption, all amid the vessel’s embrace.
- Nanotechnology: Nanotechnology befriends glass reactors, coaxing them into birthing nanoparticles and nanomaterials. The sanctity of observation paints the portrait of size, shape, and composition, the levers of control.
- Academic Research: In academic chambers, glass reactors thrive, ever at the beck and call of diverse scientific pursuits. Reactions are birthed, reaction kinetics submit to scrutiny, and theoretical models are christened with validation.
- Fine Chemicals and Specialty Materials: Glass reactors sing their siren song in the pursuit of finesse. Electronics unfurl, optical components twinkle, and ceramics traverse their paces—all beneath the glass reactor’s sanctified aegis.
- Continuous Flow Chemistry: Polymerization: Glass reactors are employed in the polymerization of monomers to produce various types of polymers. The visibility and chemical resistance of glass make it suitable for monitoring the polymerization process.
These are just a few examples of the diverse applications of glass reactors. Their versatility and compatibility with a wide range of chemical processes make them essential tools in modern research and industrial settings.
Safety, Serenaded: Precautions and Nurturing
Safety unfurls its vigilant banner, with precautions and nurturing reigning supreme:
Safety Precautions for Glass Reactors:
- Proper Training: Ensure that all personnel operating the glass reactor are properly trained in its use, including safety procedures, emergency protocols, and handling of hazardous materials.
- Personal Protective Equipment (PPE): Personal protective equipment dons its mantle—safety glasses, lab coats, chemical-resistant gloves, and enclosed footwear—the guardians of well-being in glass reactor realms.
- Ventilation: Reactions thrive within well-ventilated spaces or beneath the gaze of fume hoods, where potentially noxious mists and gases are granted no quarter.
- Temperature and Pressure Limits: A delicate dance is choreographed within the confines of temperature and pressure limits, ensuring the glass’s tranquility in the face of thermal or pressure turbulence.
- Gradual Heating and Cooling: The heating ballet unfolds gradually, mindful of sudden temperature shifts that might inflict stress fractures upon the glass. Cooling mirrors the same grace.
- Avoid Impact: Glass reactors are the aristocrats of fragility, deserving of handling with due diligence. Rough encounters lead to fractures and fractures disrupt symphonies.
- Regular Inspection: Regular inspection is the mantra, etching a vigil for scratches, cracks, and the vestiges of chemical etchings. Defects necessitate a reprieve before further passages.
- Emergency Equipment: Emergency tools—the eyewash station, the safety shower—stand sentinel, within reach, a potent response to unexpected exigencies.
- Chemical Compatibility: The compatibility tapestry unravels, preventing marriages with reactive or corrosive materials. They bode ill for the glass’s sanctity.
- Pressure Relief: Use pressure relief devices or safety valves to prevent excessive pressure buildup in the reactor vessel.
The Elixir of Nurturing: Maintenance Unveiled
Maintenance blooms as a sacred pledge:
- Cleaning: Post-reaction, cleansing takes center stage, a ritual of purging residue or taint that might cloud future reactions. Manufacturer-endorsed rituals guide the ceremony.
- Lubrication: Moving entities—stirrers, joints—revel in the embrace of lubrication, a balm against friction’s intrusion.
- O-Rings and Seals: O-rings and seals, the maestros of sealing, demand inspection and replacement as needed, custodians of a hermetic embrace.
- Calibration: Gauges and sensors embark on the journey of calibration, a pilgrimage toward accurate measurements and data sanctity.
- Glassware Inspection: The mirth of glassware inspection finds its place, examining every nook and cranny, treading the path of wear, scratches, and fractures.
- Storage: Storage unfurls as a sanctuary, sheltering the glass reactor from the clutches of harm and the burning gaze of sunlight.
- Avoid Abrasive Cleaning: The glass, a deity of elegance, shuns the abrasions wrought by harsh scrubbing. Strength remains the compromise.
- Prevent Over-Tightening: Glassware assembly and disassembly dance to a measured rhythm. Excessive force births havoc, whereas tempered strength forges longevity.
- Consult Manufacturer Guidelines: The manufacturer’s gospel, etched within guidelines, sets the compass’s bearing, guiding the symphony of nurturing.
By following these safety precautions and maintenance guidelines, you can ensure the safe and efficient operation of glass reactors and prolong their lifespan.
The Curtain Call: Embracing the Finale
In summation, glass reactors emerge as stewards of chemical exploration and industrial harmonies. Their mantle of versatility, transparency’s radiant embrace, and control over reaction conditions herald their triumph in diverse arenas. Mastery over the genres of glass reactor varieties, insight into their operational choreography, and expertise in their guardianship unfurl as prerequisites for a symphony of safe and efficacious reactions.
Inquisitive Minds Seek Clarity: FAQ Resolved
- Q: Are glass reactors suitable for high-pressure reactions? A: Yes, some glass reactors are designed to withstand high pressures and are used in high-pressure applications.
- Q: Can I use corrosive substances in a glass reactor? A: Glass reactors are resistant to many chemicals, but it’s essential to choose the right material based on the reactants used.
- Q: Can I automate the control of a glass reactor? A: Yes, modern glass reactors can be integrated with automation systems for precise control and data logging.
- Q: How do I clean a glass reactor after a reaction? A: Cleaning involves thorough rinsing with appropriate solvents and ensuring no residue is left behind.
- Q: Can glass reactors be used for large-scale production? A: Yes, certain types of glass reactors, such as continuous reactors, are suitable for large-scale production processes.
View more about Batch Reactor on Wikipedia