Exploring the Revolutionary Potential of Closed Loop Extractors in Modern Extraction Processes
In the fast-evolving landscape of contemporary extraction techniques, the closed loop extractor emerges as a true game-changer. Its revolutionary ability to streamline solvent extraction procedures, coupled with an unwavering commitment to safety and efficiency, has firmly established it as an indispensable cornerstone across diverse industries. In this comprehensive article, we will embark on an in-depth exploration of the world of closed loop extractors, unveiling their myriad benefits, operational intricacies, and extensive applications.
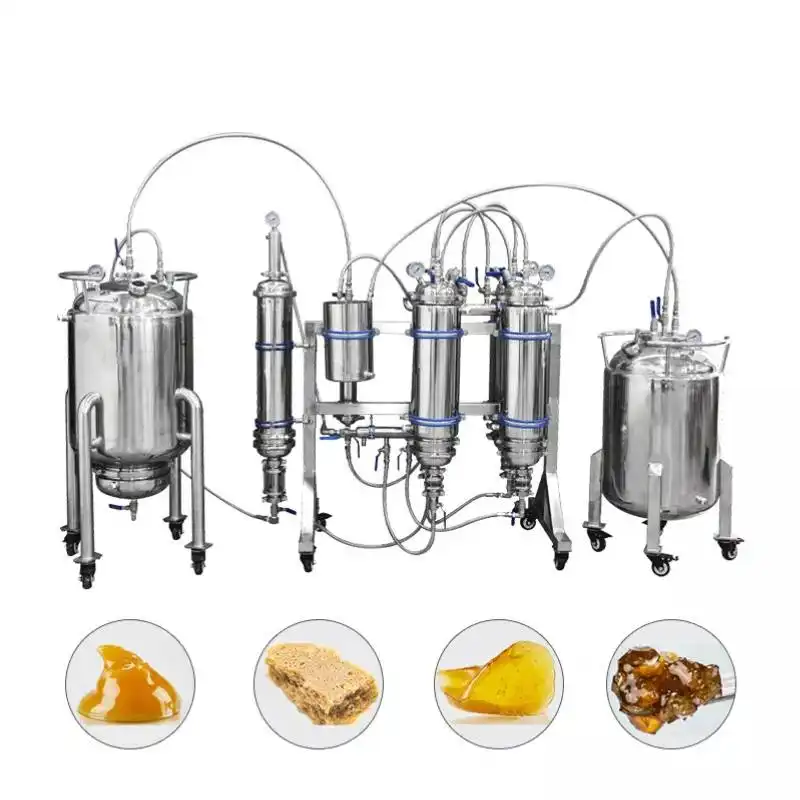
Introduction: Unveiling the Remarkable Potential of Closed Loop Extractors
In the dynamic realm of solvent-based extraction methods, closed loop extractors stand out as a pioneering advancement. Unlike traditional open extraction systems, closed loop extractors are ingeniously designed to operate within a controlled environment, effectively eliminating the release of solvents into the atmosphere. This innovative closed-loop architecture not only enhances safety measures but also significantly boosts overall operational efficiency, making it the preferred choice across a diverse array of industries.
Types of materials commonly extracted using closed loop systems
Closed-loop systems are designed to minimize waste and environmental impact by recycling and reusing materials within a controlled cycle. Several types of materials are commonly extracted or processed using closed-loop systems to reduce resource consumption and promote sustainability. Some examples include:
- Metals: Closed-loop systems are often used in metal extraction and processing, such as aluminum, copper, and steel. These systems aim to recover and recycle metals from discarded products, industrial waste, and scrap materials.
- Plastics: Closed-loop systems can recycle plastics by collecting used plastic products, processing them into raw materials, and then using these materials to create new plastic products.
- Paper and Cardboard: Closed-loop systems in the paper and cardboard industry involve collecting used paper and cardboard products, de-inking and processing them, and using the resulting pulp to manufacture new paper and cardboard items.
- Textiles: The fashion industry is adopting closed-loop systems to recycle textiles. Old clothing and fabrics are collected, sorted, and processed into new fibers for creating new clothing items.
- Electronics: Closed-loop systems for electronics involve the collection and disassembly of electronic waste (e-waste) to recover valuable components, metals, and materials for reuse in new electronic products.
- Biomass and Organic Waste: Closed-loop systems can be used in composting and anaerobic digestion processes to convert organic waste, such as food scraps and yard trimmings, into nutrient-rich compost or biogas for energy generation.
- Construction and Demolition Waste: Closed-loop systems can recover materials from demolished buildings, such as concrete, bricks, and wood, for reuse in new construction projects.
- Glass: Closed-loop systems for glass involve collecting and processing used glass containers and products to create new glass items, reducing the need for raw materials.
- Automotive Components: In the automotive industry, closed-loop systems can recycle and reuse components like engines, transmissions, and body parts from old vehicles.
- Packaging Materials: Closed-loop systems aim to recycle packaging materials, such as cardboard boxes, plastic containers, and glass bottles, by processing them into new packaging materials.
- Oil and Lubricants: Closed-loop systems can recycle used motor oil and lubricants through processes like re-refining, where the oil is purified and reprocessed for reuse.
- Water and Wastewater Treatment: Closed-loop systems in water treatment involve recycling and reusing water through processes like reverse osmosis, allowing water to be treated and reused in various applications.
These are just a few examples of the types of materials commonly extracted or processed using closed-loop systems. The goal of such systems is to reduce waste, conserve resources, and promote a more sustainable approach to material consumption and production.
The Mechanism Unveiled: How Closed Loop Extraction Works
At the core of closed loop extractors lies a brilliantly simple yet effective mechanism. The process begins with the introduction of a mixture containing both solvent and the target material into a sealed loop system. As the solvent interacts with the material, it dissolves the desired compounds, resulting in a solution. This solution undergoes a precisely orchestrated journey through a series of interconnected vessels and columns, facilitating the seamless separation of the extracted components.
Step-by-step explanation of the extraction process
- Preparation:
- Gather the necessary equipment and materials, including the Closed Loop Extractor System, plant materials, solvent (such as butane or propane), filters, and safety gear.
- Ensure that the extraction vessel, collection chamber, recovery tank, and all other components of the system are clean and properly assembled.
- Loading the Extraction Vessel:
- Carefully place the plant material (e.g., dried herbs, flowers, or other botanicals) into the extraction vessel. The amount of plant material used will depend on the desired yield and potency of the extract.
- Securing and Sealing:
- Securely close and seal the extraction vessel to ensure an airtight environment.
- Solvent Injection:
- Connect the solvent supply line to the extraction vessel and the recovery tank.
- Open the ball valves to allow the solvent to flow from the recovery tank into the extraction vessel.
- Extraction:
- The solvent interacts with the plant material, extracting essential oils and other compounds. This process typically takes place at low temperatures and under controlled pressure to preserve the integrity of the desired compounds.
- Filtration:
- As the solvent moves through the plant material, it carries extracted compounds along with it. Before reaching the collection chamber, the solution passes through filters to remove any solid plant material particles.
- Separation and Collection:
- The filtered solution enters the collection chamber, where the extracted compounds and solvent mixture is collected. The compounds may separate based on their densities, with the more dense compounds sinking to the bottom.
- Recovery:
- Close the ball valves between the extraction vessel and the recovery tank.
- Begin the recovery process by heating the collection chamber or using a heating jacket to increase the temperature. This causes the solvent to evaporate and turn into vapor.
- Condensation:
- The solvent vapor travels through the condensing coil, where it is cooled down and condensed back into liquid form.
- Solvent Collection:
- The condensed solvent drips into the recovery tank, where it is collected for reuse in future extraction cycles.
- Final Product Collection:
- The extracted compounds remain in the collection chamber once the solvent has been recovered. This concentrate or essential oil can be collected and stored for further processing or use.
- Cleaning and Maintenance:
- Properly clean and maintain all components of the Closed Loop Extractor System to ensure its longevity and safe operation for future extraction cycles.
- Safety Measures:
- Throughout the process, ensure that safety measures are followed, including proper ventilation, wearing protective gear (such as gloves and safety goggles), and adhering to guidelines for handling flammable solvents.
The closed-loop extraction process is designed to efficiently and safely extract valuable compounds from plant materials while minimizing waste and environmental impact. It requires careful attention to detail, proper equipment, and adherence to safety protocols.
Dissecting the Components of a Closed Loop Extractor System
A Closed Loop Extractor System is a specialized equipment used for extracting essential oils, concentrates, and other valuable compounds from plant materials. It’s designed to operate in a controlled environment to ensure safety and efficiency. The components of a typical Closed Loop Extractor System include:
- Extraction Vessel: This is the main chamber where the plant material is loaded for extraction. It’s typically a sturdy, pressure-rated container designed to withstand the extraction process.
- Collection Chamber: After extraction, the collection chamber holds the solvent and the extracted compounds. It’s where the mixture is separated and the solvent is recovered for reuse.
- Recovery Tank: This tank collects the solvent that has been used for extraction. It allows for the separation of the solvent from the extracted compounds through heating and pressurization.
- Condensing Coil: The condensing coil helps cool down and condense the solvent vapors back into liquid form for recovery and reuse.
- Solvent Pump: The pump is responsible for circulating the solvent throughout the system during extraction and recovery processes.
- Pressure Gauges: Pressure gauges monitor and display the pressure levels within the system to ensure safe and controlled operation.
- Pressure Relief Valve: This safety feature releases excess pressure from the system to prevent any potential hazards.
- Heating Mantle or Jacket: Some systems have a heating mantle or jacket that helps regulate the temperature during extraction and recovery.
- Filters: Filters are used to remove plant material particles from the extracted solution before it enters the collection chamber.
- Ball Valves: These valves control the flow of solvent and extracted solution within the system.
- Sight Glasses: Sight glasses allow operators to visually monitor the flow and condition of the solvent and extracted solution as it moves through the system.
- Gaskets and Seals: These components ensure airtight and secure connections between different parts of the system.
- Clamps and Fasteners: Secure fasteners and clamps hold the various components together, maintaining the integrity of the closed-loop system.
- Electrical Controls: Some systems come with electrical controls, such as switches, buttons, and digital displays, to manage temperature, pressure, and other parameters.
- Cooling System: A cooling system, like a chiller, can be used to regulate and maintain proper temperatures during the extraction process.
- Safety Features: Closed Loop Extractor Systems often include safety features like pressure relief systems, emergency shut-offs, and proper ventilation to ensure safe operation for operators.
These components work together to facilitate the extraction, separation, and recovery processes within a closed-loop environment, minimizing the risk of solvent exposure and ensuring efficient extraction of valuable compounds from plant materials.
Versatile Solvents for Varied Applications in Closed Loop Extraction
Closed loop extractors showcase remarkable versatility in accommodating an array of solvents, each tailored to specific extraction objectives. Common solvents encompass hydrocarbons such as butane and propane, as well as supercritical CO2. The choice of solvent depends on factors including target compounds, desired purity levels, and intricate regulatory considerations.
Unveiling the Plethora of Benefits Offered by Closed Loop Extraction
The allure of closed loop extractors is underscored by a multitude of enticing advantages:
- Elevated Safety Standards: The hermetically sealed system serves as an impregnable barrier against solvent exposure, ensuring the well-being of operators.
- Efficiency Amplified: Controlled conditions within closed loop extractors yield optimal solubility and extraction rates, breathing life into the concept of efficiency.
- Guardians of Purity: By minimizing contact with oxygen, closed loop extraction reduces the risk of degradation for delicate compounds.
- Eco-Conscious Approach: The reduction in solvent emissions champions eco-friendliness, leaving a greener footprint in the realm of extraction.
Applications Across Industries: The Versatility of Closed Loop Extractors
The realm of closed loop extraction extends its influence across various industries:
- Botanical Marvels: This facet involves the extraction of active compounds from plants, with applications spanning medicinal and flavor-enhancing domains.
- Aromas of Excellence: Closed loop extractors play a pivotal role in producing potent aromatic extracts that find their purpose in perfumes and therapeutic oils.
- Cannabis Chronicles: From medical marvels to recreational indulgence, closed loop extractors are key players in extracting cannabinoids and terpenes from cannabis.
- Culinary Ventures: The extraction of natural flavor compounds for culinary creations is yet another arena where closed loop extractors shine.
Navigating Essential Considerations for Successful Closed Loop Extraction
Unlocking the full potential of closed loop extractors requires a keen focus on vital factors:
- Material Mastery: The efficiency of extraction depends on factors like particle size, moisture content, and material uniformity.
- Solvent Symphony: Careful selection of the right solvent, aligned with target compounds and regulatory standards, is paramount.
- Precision in Parameters: Temperature, pressure, and flow rates must be finessed for desired outcomes to unfold.
Safeguarding Longevity and Well-Being: Maintenance and Safety Imperatives
Ensuring the sustained performance and safety of closed loop extractors mandates adherence to rigorous maintenance and safety protocols. Regular inspections, thorough cleaning routines, and precise calibration collectively contribute to consistent operation and minimal risk exposure.
The Triumph of Closed Loop Extraction: A Comparative Odyssey
A head-to-head comparison between closed loop and open extraction systems highlights the undeniable advantages of the closed loop approach, showcasing improvements in safety, efficiency, and product excellence.
Forging Ahead: The Evolution of Closed Loop Extraction Technology
As technological frontiers continue to expand, the trajectory of closed loop extraction systems is poised to embrace heightened sophistication. Anticipate the infusion of increased automation, real-time monitoring capabilities, and the tantalizing prospect of tailor-made customization.
Green Horizons: Embracing Environmental Consciousness and Sustainability
The environmental footprint of closed loop extraction resonates harmoniously with the principles of sustainability, ushering in reduced solvent emissions and a marked reduction in waste generation.
Navigating Legal Waters: Compliance and Regulations
The landscape of closed loop extraction is intricately interwoven with legal and regulatory frameworks. Navigating this terrain is paramount, as adherence to industry-specific regulations and safety standards is the cornerstone of successful implementation.
Chronicles of Success: Real-World Glimpses into the Power of Closed Loop Extractors
Embark on a journey through real-world instances where closed loop extractors have transformed extraction processes. Witness firsthand the increase in yields, enhancement of product quality, and infusion of operational efficiency.
Conclusion: A Paradigm Shift Engraved in Closed Loop Extraction
The transformative impact of closed loop extractors on solvent extraction methodologies is indisputable. This evolution paves the way for a safer, more efficient, and environmentally aligned alternative. As technological progress reverberates, closed loop extraction systems will continue to emerge as pivotal players, seamlessly catering to the demands of modern extraction practices.
Exploring Uncharted Territories: Addressing Curiosities About Closed Loop Extractors
- Are closed loop extractors suitable for small-scale operations?
- Yes, closed loop extractors are available in various sizes, making them adaptable to both small and large-scale operations.
- What safety precautions should be taken when using closed loop extractors?
- Operators should wear appropriate protective gear, ensure proper ventilation, and follow recommended protocols for solvent handling.
- Can closed loop extraction be used for heat-sensitive compounds?
- Yes, closed loop systems allow for precise control of temperature, making them suitable for extracting heat-sensitive compounds.
- Are closed loop extractors cost-effective in the long run?
- While the initial investment may be higher, closed loop extractors’ efficiency and product quality often result in long-term cost savings.
- How do closed loop extractors contribute to sustainability?
- Closed loop extraction minimizes solvent emissions and waste generation, aligning with environmentally friendly practices.
View more about Extraction on Wikipedia